How Does CR/DDA Assist the Aerospace Industry?
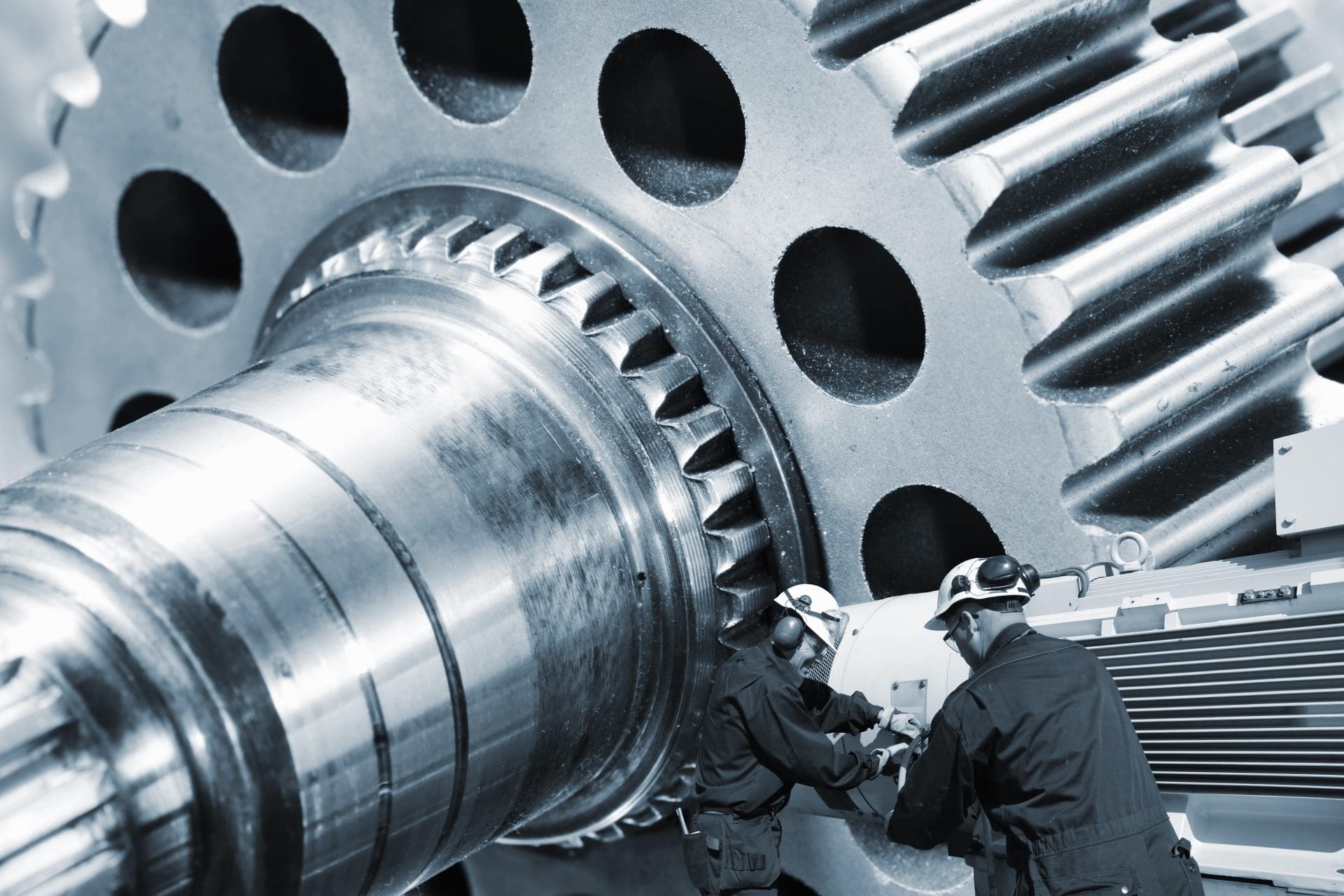
Jump to: CR & DDA in the Areospace Industry, CR & DDA Solutions
The aerospace industry demands an intense focus on precision and accuracy. When producing technology for this sector, every part must fit into place perfectly to ensure safety and long-term product durability. The aerospace industry frequently relies on production methods such as investment casting to create components for the interior, landing, breaking, cargo and hydraulic fluid systems, so component testing is essential. Ensure your business’s aerospace parts meet the highest safety and precision standards with computed radiography (CR) and digital detector array (DDA) radiography solutions from Fujifilm.
CR/DDA in the Aerospace Industry
Though investment casting is an effective method of producing advanced and complicated aerospace components, potential defects stem from the many factors that affect the mold quality and process. Through CR/DDA, businesses can verify their aerospace parts’ precision and safety through the preferred method of non-destructive testing for sub-surface defects in virtually all aerospace metals. Digital radiography has several advantages over radiographic film processing, such as its ability to reduce exposure times and acquiring images without the need for a darkroom.
Non-destructive testing methods like computer radiography allow businesses to inspect their components’ quality with digitally transferred images. CR/DDA techniques will enable your business to eliminate the lengthy film processing stage necessary for developing radiographic images and provide you with a detailed picture. Whether you manufacture welded parts or hydraulic fluid components, CR/DDA digital radiography processes allow your business to inspect your components faster and easier than the competition.
CR/DDA Radiography Solutions From Fujifilm
The FUJIFILM DynamIx HR2 System provides high-resolution radiographic readings for pitches between 25 μm and 100 μm. With the DynamIx HR2, your business can easily read complex components with high accuracy. The DynamIx HR2 fits in small workspaces and works with an insertion/ejection system that reads an IP and then ejects it from the front of the machine. This system can read IPs up to 152 cm long.
The FUJIFILM DynamIx Special Cut IP System also comes with several specialized tools for IP inspection. Fujifilm has created different IP types for the following applications:
- S Type: This type allows you to insert strip-form IPs into the slits.
- F Type: This tool features a molded portion to fit a fin-attached IP.
- Hand-held type: This instrument helps you fit an IP into the holder using your own configuration.
Beyond our CR radiography solutions, we specialize in DDA systems, including the Dynamix FXR and FXR pads. Each Dynamix FXR provides a 100 μm pitch resolution exposure designed to deliver high-quality imaging test after test. Their active 16-inch-square area makes them ideal for inspecting large and small components alike.
Trust CR/DDA Solutions From Fujifilm
Fujifilm is one of the industry’s most trusted providers of non-destructive radiography testing equipment. We understand the importance of component testing in the aerospace industry and have perfected our computer radiography and digital detector array radiography products to ensure your aerospace parts are safe. View the full Fujifilm selection of CR/DDA products and contact us about CR/DDA solutions today.