NDT Pipeline Inspections
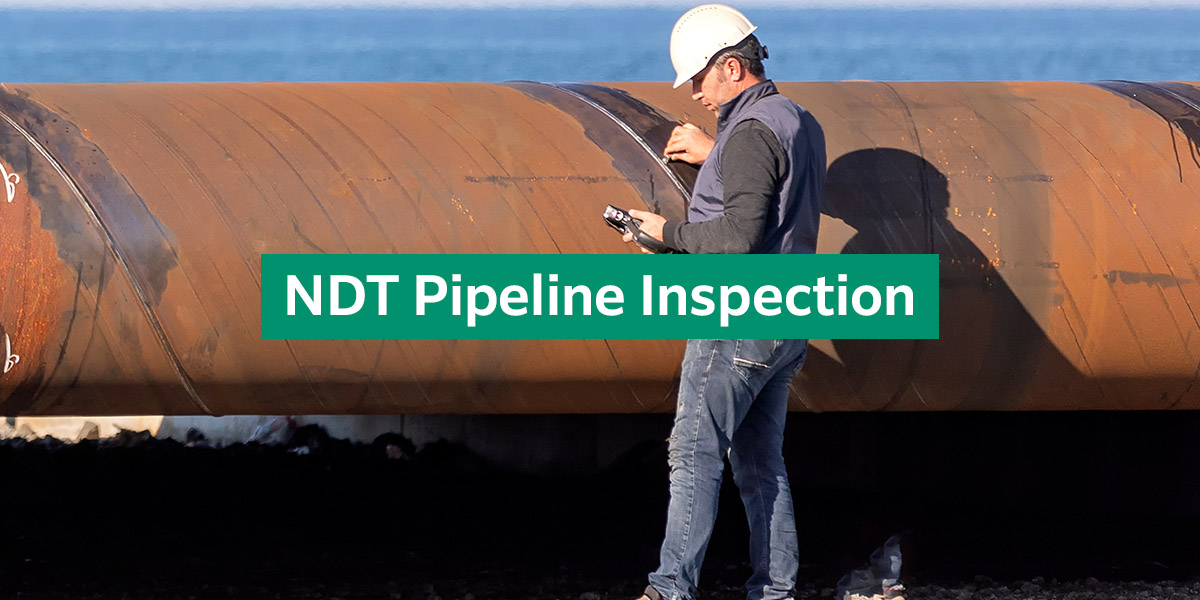
Underground pipelines are a vital part of modern infrastructure. Nearly all buildings rely on underground pipelines for water in taps, utilities such as natural gas and transportation of petroleum products and industrial chemicals.
As essential and effective as pipelines are, they are susceptible to damage. Conducting regular pipeline inspections is crucial for safety and maintaining infrastructure. Non-destructive testing (NDT) inspection methods, also known as non-destructive examination (NDE), make it possible to assess, monitor and maintain infrastructure that is otherwise all but inaccessible — and in a way that cannot cause any damage to pipelines.
NDE pipe testing allows you to test intricate underground systems with precise, affordable technology such as traditional film, computed radiography (CR) and digital detector array (DDA) radiography solutions from Fujifilm.
Why Do Pipelines Need to Be Inspected?
Pipelines carry natural and synthetic products like oil, gas, slurry, sewerage and chemicals that go from plants to storage. These various products can impact residents, workers and the environment. There are millions of miles of underground pipeline systems in the United States alone, so keeping people and the surroundings safe by ensuring that pipes do not leak or explode is crucial.
Many risks are associated with pipeline failure:
- Environmental damage: If pipes leak, harmful substances can be released into the environment. These substances can affect wildlife, groundwater and entire ecosystems.
- Property damage: Burst underground water pipes can damage a property’s foundation and lead to sinkholes. Water leaks can also cause mold.
- Safety and health hazards: Pipelines carrying toxic or flammable materials could explode under certain circumstances, such as collapsing buildings, natural disasters and equipment failure. Explosions and other catastrophic failures can cause serious physical harm and pose health hazards to citizens in the vicinity.
- Economic consequences: Pipeline failure can lead to serious economic losses with far-reaching effects. If the infrastructure fails, industries face the cost of replacing parts and rebuilding systems and financial losses due to service disruptions.
The consequences of underground pipeline failure can be severe, but industries can take proactive maintenance measures to identify issues within pipeline systems before they escalate and become emergencies.
Underground Pipe Inspection Methods
Inspectors regularly check pipelines for substance buildup, corrosion, leaks, cracks and other concerns that could lead to system failure. Testing the pipelines also ensures that systems meet safety and compliance standards. A company’s testing methods must be non-invasive to protect the system’s integrity and keep inspectors safe. NDT methods provide the answer. Different NDT inspection techniques include:
- Radiography: Radiographic testing (RT) employs radiographic film, combined with Computed Radiography and Digital Detector Array technologies, for NDT inspections. X-rays or gamma rays penetrate the pipeline structures while under observation, and inspectors can observe the recording on a radiographic plate for further testing. RT is accurate, provides a permanent visual representation, can be used to test any material and is time-effective as no surface preparation is required.
- Ultrasonic: Ultrasonic NDT equipment is similar to the ultrasound machines at a doctor’s office. This method uses high-frequency sound waves to find defects in pipelines. This method is consistent, delivers instant results and can detect surface and subsurface defects. However, it is also expensive, requires extensive training and works better for some materials than others.
- Eddy current: Eddy current testing uses specially designed coils to create changing magnetic fields that permeate conductive materials to pick up on defects. It is an excellent method for finding surface defects and defects in multi-layer structures. However, eddy currents are only effective on conductive materials, require careful interpretation of the results to eliminate non-relevant indications and leave no permanent record unless the process has been automated.
- Magnetic particle: Magnetic particle testing works for ferromagnetic stainless steel pipes. The method is used for surface identification only. It can detect linear flaws on the surface, find areas that may crack or break, and detect poor joints. While this method is inexpensive and gives an immediate indication of defects, it only works for ferromagnetic materials and can only examine small areas of a surface at a time.
- Acoustic emission: Acoustic emission testing uses sensors to record elastic ultrasonic waves traveling through solid objects to find defects in the material. The method is straightforward and inexpensive. However, it is only suitable for solid materials like concrete, making it inappropriate for pipelines.
While all these methods have particular strengths, radiography is fast, precise and more accessible than other methods.
FUJIFILM Industrial X-Ray Film
You can use various technology and equipment for radiography for pipeline inspections. One of the most common and straightforward methods is traditional film radiography. Essentially, you take an image using traditional X-ray film and expose it to radioactive waves to produce an image of the object.
FUJIFILM Industrial X-ray Film for oil and gas provides a consistent non-destructive testing method. Featuring innovative film technology, FUJIFILM Industrial X-ray film produces high-quality images and is compatible with all NDT chemistries.
CR/DDA
CR is a form of digital radiography that uses imaging plates that respond to radiation in place of film. An inspector will take a radiographic image, and a CR reader will scan the imaging plate and convert it to a digital image. Inspectors may use diagnostic imaging software to view the image, improve it and analyze it.
A DDA is an electronic device that converts ionizing radiation from X-rays or gamma rays into electrical signals. It then digitizes these signals with the help of software so inspectors can transfer the data to a computer and view an image of the data. DDA is advantageous as the image requires little to no processing, providing immediate results.
CR/ DDA is beneficial for pipeline expectations for several reasons. These technologies provide results quickly and are accurate, safe with proper training, affordable and accessible, especially compared to other NDT methods.
Fujifilm’s NDT Solutions for Pipeline Inspections
When you need to conduct fast, accurate and convenient non-destructive testing for pipeline inspections for pipeline systems, you can rely on Fujifilm. As an industry leader in NDT imaging technologies, we offer a wide selection of NDT hardware, diagnostic software and accessories for NDT processes across industries.
We also offer premium solutions, including training services provided by an expert team. Contact us today to learn more about our digital and traditional radiography equipment for NDT pipeline inspection solutions.