What Is Destructive Testing?
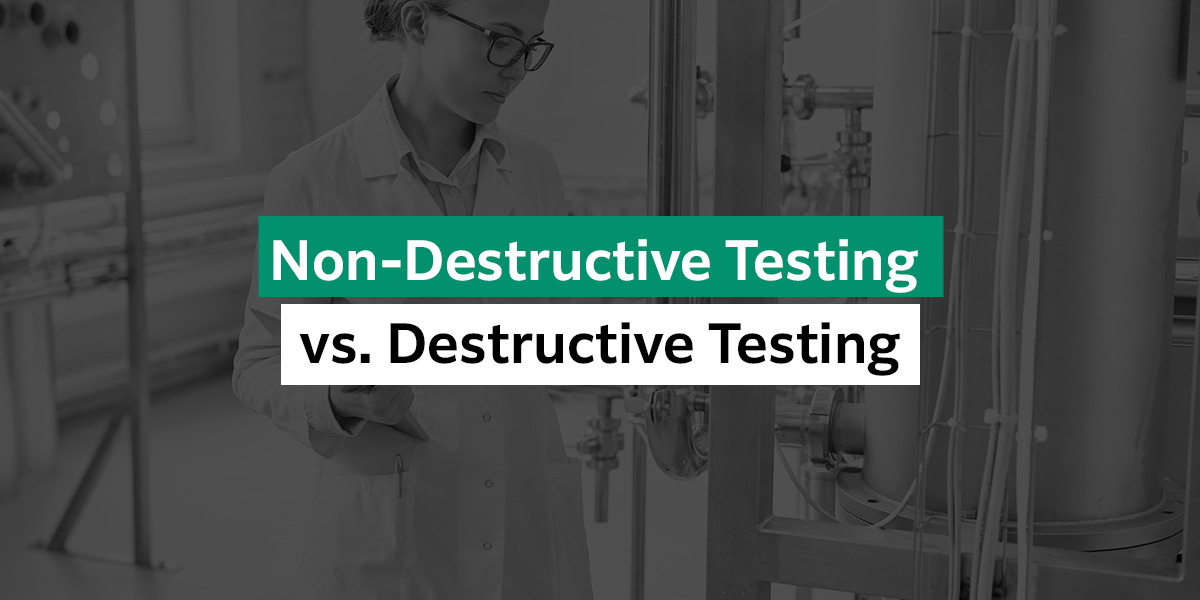
Jump to:
- What is Destructive Testing?
- Destructive Testing Methods
- Destructive Testing Applications
- Drawbacks of Destructive Testing
- What is Non-Destructive Testing?
- Advantages of Non-Destructive Testing
Destructive testing (DT) and non-destructive testing (NDT) are distinct methodologies for assessing the durability of an item. DT explores the pressure limits by pushing components to their breaking point, providing insight into potential failure modes.
Conversely, NDT inspects items without causing any lasting harm, making it the preferred method for gauging a material’s endurance while maintaining its integrity. While both methods supply crucial data, NDT is increasingly favored for its efficiency and non-invasiveness.
Businesses must understand the difference between NDT and DT to ensure they are using the correct method for quality control processes.
What Is Destructive Testing?
Destructive testing is a test method used to understand the performance or behavior of a machine, component, or material by determining its exact point of failure. The term “destructive” means that the specimen in question undergoes continuous stresses until it eventually fails, either by material deformation or destruction. The testing process can either follow specific procedures or be geared to generate particular service conditions.
In most cases, destructive testing methods test components before mass production begins. Destructive tests give original equipment manufacturers (OEMs) an idea of their products’ limits to administer the necessary machine maintenance and operating recommendations.
Destructive tests often detect failures using equipment such as:
- Cameras: High-speed cameras enable the test operator to identify a malfunction by recording continuously until its attached sensors detect the failure. After the failure, the camera will stop recording, and the operator can review the images in slow motion to determine what happened before, during, and after the destructive event.
- Sound detectors: These devices convert sound waves and vibration from the test object into electrical signals. They then transmit these signals to the camera to set the camera into motion.
- Stress gauges: A stress gauge is a sensor that measures the amount of stress the test object experiences when a force is applied. Like a sound detector, this device converts this data into electrical signals to stop and start the camera’s recording function.
Because destructive tests result in irreversible damage, the tested item and its parts cannot be reused in regular operation after enduring destructive testing. Although the item is beyond recovery after testing, this method still has legitimate use cases.
Machines have physical and chemical properties that aren’t appropriate for all working conditions. For example, metals that are prone to corrosion are not well-suited for use in humid environments. Destructive testing helps producers identify these incompatibilities and potential drawbacks, which can prevent failure for end users.
While this test method is a regulatory requirement in some industries, including aerospace, automotive manufacturing, and infrastructure, companies are increasingly turning to non-destructive testing methods.
Types of Destructive Testing
There are various types of destructive testing that organizations use to evaluate material quality and performance. Each destructive testing method has specific case uses and follows particular standards and practices.
Though there are several types of destructive testing, the following tests are some of the most commonly used.
Corrosion Testing
Corrosion testing is used to evaluate the effectiveness of corrosion-resistance measures to prevent metal components from rusting, tarnishing, and pitting in diverse environments, including freshwater and seawater settings. According to the American Society for Testing and Materials (ASTM), destructive corrosion tests examine a material’s susceptibility, behavior, and extent of resistance to various types of corrosion.
Fracture and Mechanical Testing
Fracture testing refers to measures of resistance to the extension of a crack. Fracture mechanical testing methods examine the effects of flaws on a material’s load-bearing capacity and toughness.
Fracture and mechanical testing methods include various destructive tests, including:
- Tension tests: Tensile testing applies a pulling force to the test object to measure how well it responds to sustained tensile stress. This method helps determine mechanical properties such as ductility and yield strength.
- Charpy impact tests: This testing method puts high strain on an object to determine the amount of energy it will absorb during a fracture.
- Peel and chisel tests: Also called a peel test, this method determines weld size and failure type by applying a peel force to the joint.
- Crush testing: This testing method applies compressive force to an object to determine its maximum load capacity before failure.
- Bend tests: A bend test identifies the point of embrittlement by bending test materials in various directions.
- Pellini drop weight testing: This test establishes an object’s nil-ductility transition temperature (NDTT), which is the temperature at which a material will break during an explosion bulge test without deformation.
- Pressure testing: Sometimes called hydrostatic testing, this testing method explores how much internal pressure an object can withstand before leakage occurs.
- Fracture testing: This test applies force to a weld to reveal imperfections such as incomplete penetration, porosity, lack of fusion, and cracking due to an incorrect width-to-height ratio.
These types of destructive testing are used under different temperatures and strain rates to evaluate fracture toughness, static behavior, strength, and cyclic behavior in pressure performance, creep, and seawater environments. The results of these destructive tests can help assess and validate material integrity.
Aggressive Environmental Testing
This destructive test type uses fracture and fatigue testing to measure a machine’s effectiveness in corrosive environments, such as sour and sweet conditions, under various pressures and temperatures. Through aggressive environmental testing, users test materials based on the characteristics of their intended operating settings.
For example, when testing building materials for a beach house, you’d use aggressive environmental testing to ensure that it could withstand the humidity, high winds and salinity typical of coastal areas.
Fatigue Testing
Fatigue testing is a type of mechanical destructive test used to generate data on crack growth and fatigue life, identify areas susceptible to fatigue, or demonstrate structural safety. These evaluations determine a welded joint’s ability to endure cyclic fatigue loading conditions in either air or seawater environments.
Fatigue testing is often used on components for full-size test articles like aircraft and automobiles. It’s also used for fatigue crack growth testing on base metals, heat-affected zones and welds.
Residual Stress Measurement
Residual stress is stress distribution present in a component, structure, sheet, or plate without the application of an external load. These stresses can lead to:
- Plastic deformation
- Warping
- Fracturing
- Fatigue
- Distortion
Residual stress measurement determines whether a material can withstand extreme load conditions throughout its intended service life. These destructive tests allow engineers and designers to assess crucial component flaws and generate critical assessments.
Tensile Testing
Tensile testing, also known as elongation testing, is the process of applying controlled forces to a test material until it fails. Through this destructive testing method, the specimen is elongated or compressed based on the applicable measurement characteristics to determine the material’s strength. With these results, you can discover which materials will perform well under excessive amounts of force.
Properties you can assess through tensile testing include:
Destructive Testing Applications
Destructive testing methods have long been a reliable source for testing specimen failure. Numerous industries utilize the destructive testing of materials in all of the following applications:
- Earthquake testing: Destructive tests can evaluate how large structures like buildings will perform during earthquake events. These evaluations often take place on a shake table, which produces a similar movement to an earthquake.
- Software testing: You can use destructing testing to test a software’s robustness and stability. By causing the software to fail, you can establish range limits accordingly to ensure reliable operation.
- Automotive testing: Crash tests are a type of destructive testing designed to ensure safe vehicle design standards, such as crash compatibility and crashworthiness, by subjecting an automobile to crash conditions.
- Aircraft testing: It is standard to use destructive testing to evaluate passenger and military aircraft production models by loading components until they fail.
- Fabrication validation: Manufacturing validation is the process of ensuring that a product will satisfy certain criteria based on its service conditions and time between failures.
- Materials characterization: Destructive testing methods help measure a material’s properties and structure in the materials science field. They give valuable insights into why certain substances exhibit different behaviors and characteristics.
- Failure investigation: Failure investigation through destructive testing is used to improve asset performance by identifying the causes of failures and understanding the primary elements of these failures.
- Safety equipment evaluation: Destructive testing is used in the occupational health and safety industry to confirm the protective capacities of safety equipment under physically demanding conditions. For example, certain personal protective equipment (PPE) requires certification under International Electrotechnical Commission (IEC) and ASTM standards, which use destructive test methods.
- Hazard identification and safety assurance: Some projects require destructive testing to ensure that workplace structures and machinery will not fail and pose safety hazards when used within their limits.
Drawbacks of Destructive Testing
Though destructive testing is known for its reliability and accuracy, it also has its downsides. If your company is considering performing destructive tests to evaluate your materials, machines or components, you should first understand the drawbacks of doing so.
Resource Waste
When using destructive testing to discover a material’s performance flaws, you must destroy every item you test — that means you may demolish a machine’s vital components or its entire infrastructure. Because destructive tests deem products unsalvageable after testing, you cannot use them again in the future. While some view these losses as necessary, others see them as unnecessary material waste.
High Expenses
Because destructive tests completely destroy test specimens, they result in significant expenses for the companies conducting them. These businesses lose money from material costs and must forfeit more funds to replace them. These expenses can be particularly severe when testing larger infrastructures that cost upwards of millions of dollars.
Due to its weighty costs, destructive testing is only suitable for companies with plentiful materials that can afford to waste and replace resources.
Time Requirements
Destructive material testing is a time-consuming process compared to other testing methods. Because these types of tests involve manual processes, they’re not as efficient as automated methods. Destructive tests also require extensive prep and prolonged inspection times. Companies must also shut down job site operations to administer testing, leading to increased downtime.
Distance Limitations
When conducting destructive tests, inspectors must interact directly with the test specimens. Due to these hands-on procedures, you cannot use destructive methods to detect machine flaws across long distances as you could with other test types.
Non-Destructive Testing vs. Destructive Testing
Contrary to destructive testing, non-destructive testing (NDT) is a set of examination methods that enable inspectors to collect data and evaluate systems, materials or components without causing permanent damage. However, both destructive and non-destructive tests are used to pinpoint a test item’s defects.
Types of Non-Destructive Testing
Non-destructive testing is an umbrella term that encompasses many testing methods. Some of the primary non-destructive testing techniques include:
- Acoustic emission testing: This tactic detects short bursts of ultrasound discharged from active cracks beneath a load and evaluates their arrival time, intensity and location to identify potential problems.
- Visual testing: Through visual testing, inspectors gather visual data regarding a material’s status either by looking at the test specimen or using remote visual inspection devices for more in-depth results.
- Magnetic particle testing: Non-destructive magnetic particle testing involves identifying material flaws by observing disruptions in magnetic field flow. Through this method, inspectors induce a magnetic field in the asset and position iron particles over its surface to reveal visual defects.
- Ultrasonic testing: Inspectors transmit high-frequency waves to a material to evaluate property changes and spot surface imperfections.
- Radiography testing: This technique uses X- or gamma-radiation to pinpoint flaws by sending radiation into an asset and observing results on a shadowgraph.
- Leak testing: If a vessel leaks, you can use leak testing to determine where the defects lie.
- Liquid penetrant testing: Liquid penetrant testing uses a dye to visually reveal any issues and a fluorescent light to further examine them.
- Eddy current testing: This electromagnetic testing method is used to measure a material’s magnetic field for the strength of eddy, or electrical, currents to locate defects.
Which Industries Use Non-Destructive Testing?
Non-destructive tests are the ideal methods for testing assets across practically every industry:
- Medicine
- Art
- Oil and gas
- Electrical engineering
- Aerospace
- Chemicals
- Petroleum
- Forensics
- Power generation
- Mining
- Automotive
- Maritime
- Mechanical engineering
- Construction
Advantages of Non-Destructive Testing
Non-destructive testing methods are increasing in popularity due to the advantages they offer over destructive testing. If you’re debating whether to conduct non-destructive or destructive tests for your company, consider the following benefits of NDT.
Reduced Material Waste
Perhaps the greatest benefit of non-destructive testing is that this process leaves the test sample completely functional while still providing useful insights. That means less wasted resources. Unlike destructive testing, you don’t have to dispose of your materials after testing them. This factor is particularly beneficial for companies testing expensive or limited materials, as they won’t suffer any considerable losses.
Cost Efficiency
Objects that undergo non-destructive testing are intact and fully operational after the test, which enables you to eliminate or significantly reduce material and replacement costs. In contrast, destructive testing requires you to endure losses because it results in an unusable object.
Using non-destructive testing to identify potential machine problems before malfunctions occur will also save you money by preventing costly equipment repairs and replacements in the future.
Minimal Downtime
Non-destructive processes are highly efficient and take considerably less time to perform than destructive testing. That’s because NDT eliminates the need to break down materials for testing purposes or perform repeated manual tests.
You can also test materials while they’re still in use, meaning you won’t have to cease operations during testing. As a result, you’ll minimize downtime and reduce operating costs.
Increased Safety
When your systems function as they should, you maintain a safe and secure work environment. Non-destructive testing helps companies identify potential issues and determine whether components require improvements or repairs. These tests help you prevent accidents on the job site by ensuring machines operate safely.
Reliable Results
Non-destructive tests detect material defects with high accuracy, producing reliable results. Using these outcomes, you can gain valuable insights regarding product performance and behavior and make adjustments as needed. With more reliable testing and modification comes better product manufacturing.
Leverage the Advantages of NDT With Fujifilm
Experience superior non-destructive testing imaging quality through state-of-the-art solutions from Fujifilm. Our NDT equipment, including film, digital detector arrays (DDTs), and computed radiology (CR) solutions, produce clear images that you can easily view on our innovative software. We’re proud to provide top-quality products and services that help to advance the industrial sector while improving workplace safety and environmental protection.
Choosing Fujifilm as your go-to NDT imaging solutions provider will help you reduce inspection downtime and unnecessary material waste while improving the performance and quality of products. We also offer training programs so your team can learn how to meet the applicable industry requirements.
Contact us to inquire about our non-destructive testing solutions today!