What Is Acoustic Emission Testing?
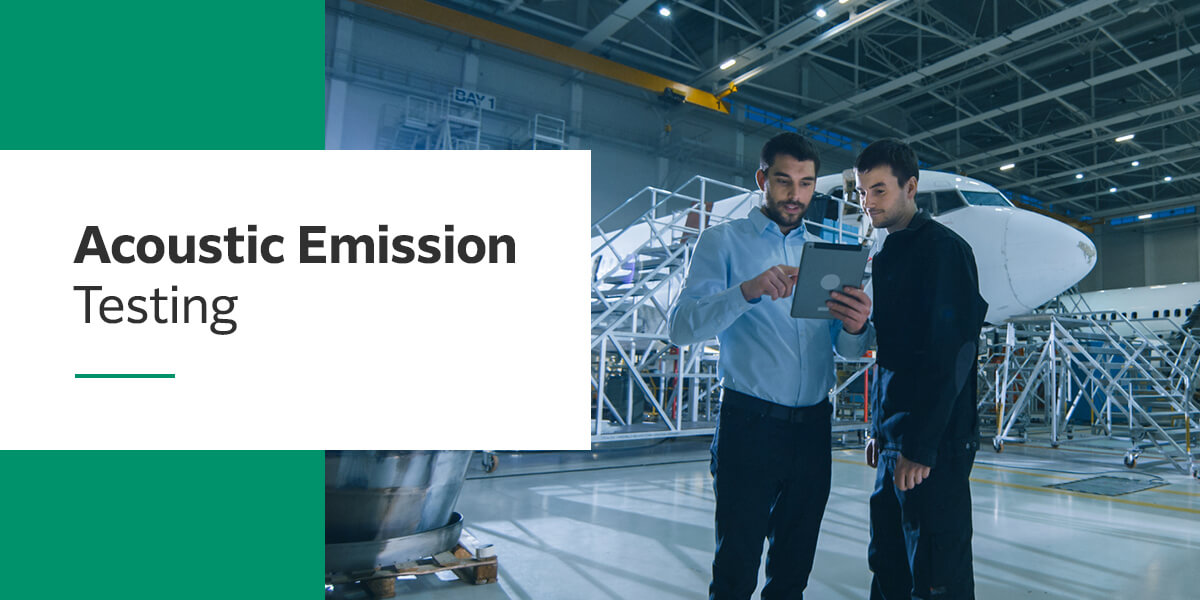
Jump to:
- Types of Acoustic Emissions
- Applications of Acoustic Emission Testing
- Acoustic Emission Testing Advantages
- Acoustic Emission Testing Limitations
Acoustic emission testing (AET) is a non-destructive testing (NDT) technique that monitors ultrasonic stress waves within the test object through a set of connected sensors. While it’s an effective method for detecting flaws in an object, it’s important to understand its applications and limitations to determine whether it is the right technique for a specific use case.
This guide explains everything you need to know about AET and what it’s used for.
How Does Acoustic Emission Testing Work?
AET uses a system of sensors and software to record and analyze ultrasonic waves in or on a solid object, like a machine component. The wave will change speed and amplitude any time it encounters a defect.
After collecting this data, the sensors convert the waves into electrical signals and relay them to an external processor for analysis. Inspectors look for any changes in the ultrasonic wave, which indicate the presence of a defect.
The amount of damage a component has sustained is directly proportional to the release of ultrasonic energy detected in the test. That means that if you test the acoustic emissions of a component with extensive fractures, the test results will display this damage as spikes of ultrasonic energy.
But first, why should you use non-destructive testing methods? Destructive testing methods cause irreversible damage to the component undergoing testing, meaning you will need to replace it. However, because NDT methods assess parts without causing damage, you can reuse the component after testing.
Types of Acoustic Emissions
The term “acoustic emissions” refers specifically to the transient elastic waves created from events of rapid energy releases within a material. These waves, also known as sound waves, can come from a wide range of events, which include:
- Fiber breakage
- Debonding
- Thermal stress
- Phase changes
- Crystalline distortions like twinning
- Objects cracking under stress
- Dislocation resulting from plastic deformation
There are two primary types of acoustic emissions:
- Burst: A burst is a short emission that results from distinct individual events.
- Continuous: Continuous acoustic emissions are sustained signals resulting from one or more overlapping or successive sources.
The type of emissions an object generates depends on several factors, such as the object’s unique material properties and the level of stress it is under.
Acoustic Emission Testing Methods
You can use several different acoustic emission testing procedures to analyze objects. Each technique serves a different purpose:
- Proof testing: Proof testing demonstrates that a component can withstand a certain degree of pressure by gradually increasing the load on the component. The absence of significant emissions determines a successful result.
- Fatigue testing: This testing method estimates the maximum useful life span of an object by applying a cyclic load and monitoring the emissions produced within the object.
- Failure testing: Failure tests determine the load at which an object’s structural integrity begins to fail. Like a proof test, failure tests involve gradually increasing the load on the object. However, failure tests go a step further by continuously increasing the load until the emissions readings indicate imminent failure.
- Global screening: This method evaluates the conditions of all system components under increased stress levels. The test involves gradually increasing thermal or pressure stress levels to slightly above normal and monitoring how the system functions under these conditions. Global screening aims to reveal any unknown flaws within the system that could worsen over time.
- Ongoing emission monitoring: By monitoring acoustic emissions under normal operating conditions, you can keep an eye on the damage progression of the system without needing to artificially increase stress levels. This method can help you track the condition of any previously discovered flaws so you can quickly address serious issues.
Common Acoustic Emission Testing Applications
Acoustic emission testing is versatile, with use cases across various industries, including automotive, nuclear power, aerospace, manufacturing and infrastructure. Some key applications of AET include:
- Preventive maintenance: AET is useful for testing the function and condition of machinery across multiple industries. For example, facilities that use rotating machinery can detect early wear in gearboxes and bearings with AET. It’s also helpful in detecting partial discharges in electrical machinery components like transformers and bushings.
- Structural inspection: AET is a useful way to evaluate structural integrity because it allows you to detect weaknesses before they become more significant problems. You can use it for composite, concrete and metallic structures.
- Process evaluation: You can use AET to evaluate the efficiency and success of your processes, such as assessing build quality in additive manufacturing during regular operation. Other examples of using AET to evaluate operational processes include evaluating particle impact, determining friction levels within systems, and detecting leaks in pipes and other high-pressure components.
- Emergency detection: Recent research suggests emergency response organizations may be able to detect earthquakes before they happen, which could help companies in earthquake zones minimize damage by taking proactive measures. However, this application is still developing.
Acoustic Emission Testing Advantages
AET is a practical testing choice for a variety of reasons:
- Flexibility: Depending on your application’s requirements, you can conduct AET in a lab or in-field. You can even conduct AET remotely, which allows you to test even in hazardous environments like high temperatures, high pressure, and even corrosive or nuclear environments.
- Reduced downtime: Acoustic emission testing is non-destructive and non-invasive, so you can conduct tests while the component is in normal operation. This flexibility helps maximize uptime by keeping operations running smoothly, even during testing.
- Versatility: AET can detect many different types of damage before they can disrupt your operation, including cracking, corrosion, delamination, friction, fiber breakage, and more.
- Readability: You can differentiate between the different sources of damage you detect based on their unique acoustic signatures. So if there are multiple flaws within your component, you’ll be able to tell how severe each one is.
- Reliability: AET allows you to detect damages that other NDT techniques, like dye penetration or leak testing, may not have the capacity to find.
Acoustic Emission Testing Limitations
The main limitation of AET is that it can only produce qualitative results. While the test determines that flaws exist, it cannot provide any quantitative data regarding those flaws. Some other drawbacks to AET include:
- Limited detection capabilities: AET can only detect active flaws. While stagnant defects may be present, you won’t be able to pick them up during testing because they will not produce acoustic emissions.
- Background noise interference: Getting clear results in loud environments is difficult because background noise can affect your readings. Using noise reduction technologies and signal discrimination techniques is essential for achieving precise emissions measurements.
- Initial costs: You’ll need to purchase specialized acoustic emission testing equipment to perform inspections, which can be costly. Investing in operator training is also critical for ensuring your team is experienced in using both AET hardware and software.
Enhance Your Non-Destructive Testing Procedures With Fujifilm
With decades of experience in various non-destructive testing applications, Fujifilm delivers innovative, effective imaging products for use in industries like aerospace, automotive, manufacturing and more. Our NDT equipment offerings include a range of digital radiography devices in addition to conventional X-ray imaging products.
If you’re looking to develop your workforce’s skill set, we also provide comprehensive Digital Radiography NDT training courses to prepare your employees for certification. We offer scheduled regional classes for employees at multiple experience levels and on-site training for operations wishing to provide a more individualized, hands-on experience.
Browse our non-destructive testing products and services to learn more about our products and services, or contact us today to discuss your NDT needs.