An Essential Guide to Signal-to-Noise Ratio
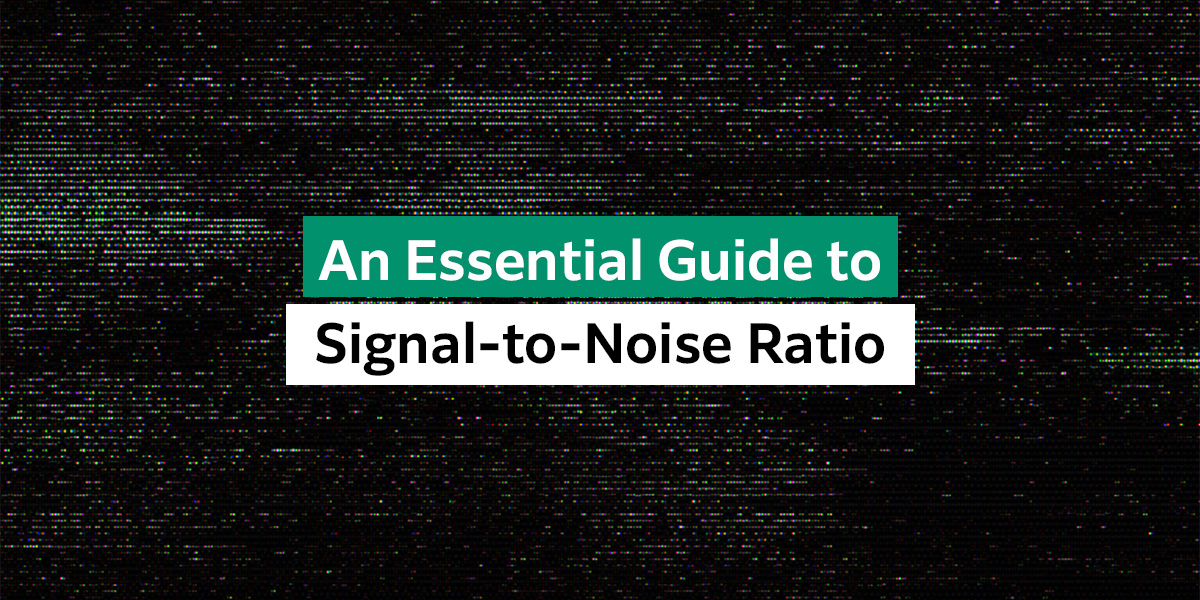
When inspecting parts and finished products for internal flaws, you need to ensure your testing methods deliver accurate results. Nondestructive testing (NDT), also called nondestructive evaluation (NDE) or nondestructive inspection (NDI), uses various methods, from acoustic testing to X-ray imaging. Whichever method you use, one mathematical calculation is essential for verifying reliable results.
Signal-to-noise ratio is a critical consideration in various NDT methods. Whether you test in-house or outsource these processes to external NDT service providers, your company must be aware of signal-to-noise ratio and its effect on test results.
This post explores what signal-to-noise ratio is, why it matters and how your manufacturing business can use this information to enhance your NDT techniques.
What Is Signal-to-Noise Ratio in Nondestructive Testing?
A simple definition of signal-to-noise ratio (SNR or S/N ratio) is the measure of a signal’s strength compared to other undesired signals, known as noise.
The basic signal-to-noise ratio formula is the signal power (P_s) divided by the noise power (P_n):
- SNR = P_s/P_n
The higher the SNR, the clearer the signal — and, therefore, the easier it is to identify flaws in the test object. In most applications, the minimum required SNR to reliably identify a flaw is 3-to-1. For comparison, the minimum for comparable testing in humans is 10-to-1.
You can calculate the SNR for various types of NDT, including:
- Radiography
- Ultrasonic testing
- Acoustic emission testing
Note that your specific parameters will vary depending on the type of NDT you use and the specific objects you are testing. For example, in acoustic or ultrasonic testing, you will use decibels (dB) as the measurement unit.
SNR vs. CNR
SNR is similar to contrast-to-noise ratio (CNR), which measures how well a signal stands out from the background. The higher the contrast in an image, the more it helps NDT technicians detect and diagnose flaws in the test object.
Like with SNR, a higher CNR is better for identifying defects during quality control. The better your CNR, the clearer and more contrasting your image — and the more reliable your findings will be.
In essence, CNR measures image clarity and contrast while SNR measures signal strength.
Why Is SNR Important?
The main reason SNR is so important in NDT is that it indicates how easy it will be to detect defects in a test object. The higher the SNR, the stronger the output, which could be an image or a measurement of an electrical signal or sound. A stronger output naturally means the defect will be easier to discern as well.
Some of the other reasons SNR is an important measurement include:
- Inspection quality: A high SNR produces a stronger output, which improves your ability to identify flaws and increases your inspection reliability.
- Data interpretation: A higher SNR makes it easier to interpret data collected during inspections, which is important for making informed decisions.
- Continuous improvement: NDT technicians can use SNR data to optimize testing parameters, which can minimize noise and enhance detection capabilities.
- Cost savings: A high SNR increases the chances of correctly detecting defects in the test object, helping minimize the need for repeat inspections and unnecessary repairs.
Signal-to-Noise Ratio in Radiography
Radiography is an NDT technique used for detecting internal flaws in structures and materials. It’s used in many different industries, including aviation, manufacturing and construction.
In radiography, SNR specifically refers to the strength of a signal in a specific region of an image compared to the surrounding noise. The less noise is present in an image, the more accurate your findings are likely to be.
SNR in Digital and Computed Radiography
Direct digital radiography (DR) and computed radiography (CR) are two NDT radiography techniques that have replaced traditional X-ray film imaging in most applications.
In DR, image data is transferred immediately to a computer without requiring an intermediate storage medium such as a disk or cassette. In comparison, CR requires a multi-stage transfer process that involves external storage media.
SNR is an essential consideration for both testing methods, as it can help you understand how much noise could have affected an image scan and potentially pinpoint the source of that noise.
For example, you might discover through SNR analysis that electromagnetic interference (EMI) from nearby devices could be introducing noise into your imaging. You can then take action to eliminate the source of the EMI and enable your team to collect more accurate images.
Precision Measurement in Radiography
Precision measurement refers to your ability to accurately and consistently measure specific characteristics of test objects using radiographic techniques.
Precise measurements are essential for achieving the most accurate NDT results possible. Whether you find internal flaws or you can approve the test object for use, precision enables you to ensure your testing is reliable for use at scale.
The Types of Noise in NDT
Depending on the NDT method used, operators might experience different types and sources of background noise.
While there are many different kinds of noise, some of the most common sources of noise in radiography include:
- Environmental factors: External conditions, including high temperatures and EMI from nearby transmitters, can add noise to the imaging system.
- Processing noise: In some cases, improperly calibrated image enhancement tools can cause distortion and artifacts to appear in a testing image.
- Scatter radiation: Secondary radiation can reflect off nearby structures, causing the light to scatter before it reaches the machine’s detector. This kind of noise can make it difficult to distinguish between different parts of an image.
- Motion artifacts: Vibrating equipment can cause movement within the image, introducing noise and artifacts such as streaks and blurring.
Noise Reduction Techniques
Some effective techniques for reducing noise in radiographic NDT include:
- Shielding and grounding: This technique involves using barriers and grounding devices to reduce EMI and produce clearer images.
- Filtering: This technique removes undesired frequencies from the environment to increase SNR and reduce background noise, strengthening the desired signal and creating a clearer picture.
- Averaging: This technique increases SNR in a test by taking the average of multiple images. Because the noise is random, the fluctuations even out more the more images you average.
Why Trust Us?
At Fujifilm, we’ve been working with imaging technologies for decades. While our business began with film photography, we quickly began diversifying into industrial technologies like X-ray testing and computed radiography.
We’re a pioneer in the imaging space, which has enabled us to lead the industry in developing safer, more efficient testing methods that enhance testing accuracy and speed. With so much experience behind us, we’re a reliable source of information on various technologies, including those in the NDT space.
Buy Effective NDT Materials From Fujifilm
If you’re looking for a reliable radiography solution for your nondestructive testing requirements, Fujifilm has what you need. Our industry-leading products include computed radiography systems, diagnostic imaging software, digital detector array panels and much more.
We also offer various levels of NDT training courses to ensure your team has the necessary qualifications to meet inspection requirements and ensure reliable results.
Contact us today for more information about our radiographic NDT solutions.