What is Magnetic Particle Inspection in NDT?
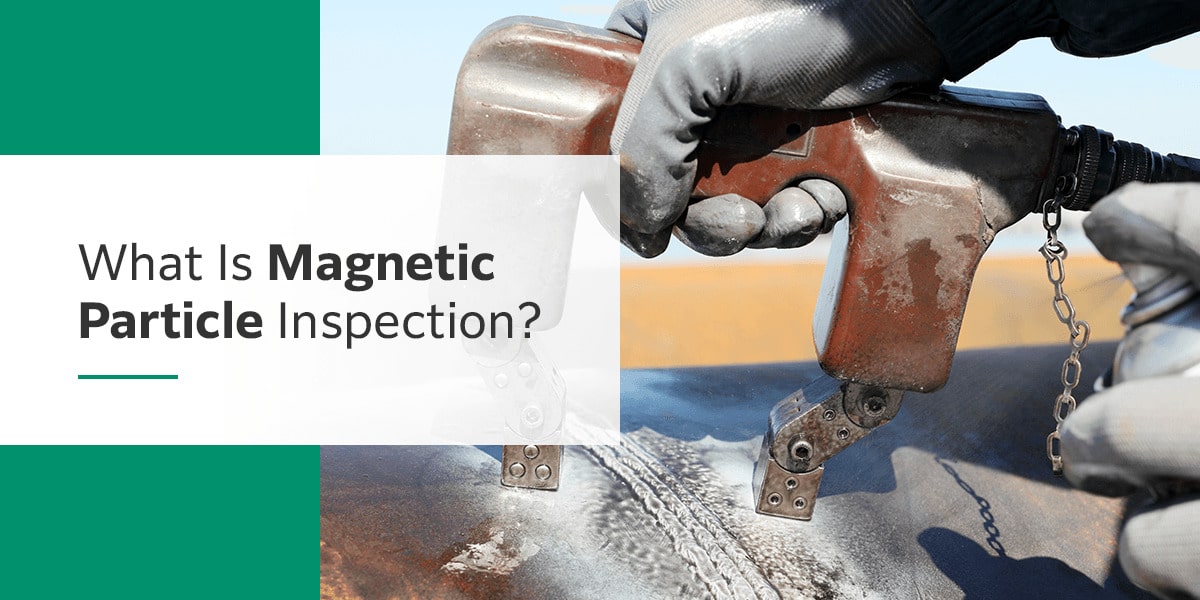
Jump to:
- How Does Magnetic Particle Inspection Work?
- Types of Magnetic Particle Testing
- Advantages of Magnetic Particle Inspection
- Disadvantages of Magnetic Particle Inspection
In the world of non-destructive testing (NDT), magnetic particle inspection (MPI) is a commonly used method to gauge the quality of a part or structure. This approach is relatively simple compared to other methods and can offer comprehensive results. Learn more about MPI, its testing types and the benefits and disadvantages to determine if it’s the right inspection method for your next project.
How Does Magnetic Particle Inspection Work?
In a magnetic particle inspection, a magnetic current is applied to the inspection material. Technicians perform this initial step by using a range of magnetization techniques. Common techniques include using an electromagnetic yoke to create electrical currents, current flow probes, adjacent cable and a permanent magnet. These techniques fall under direct or indirect magnetization.
For direct magnetization, the technician passes the magnetic current through the material to be tested. Indirect magnetization requires the technician to create a magnetic field from an outside source rather than applying a magnetic current directly through the material. Once the magnetic current is applied, it travels through the material and indicates any defects based on its behaviors.
If a material is free from defects, the magnetic field will transfer throughout without interruptions or discontinuities. If there are defects, the magnetic field gathers at the defective point and spreads out from there. These distortions become flux leakage fields, which are secondary to the initial magnetic field the technician created.
After the magnetic field has been applied, the inspector will apply magnetic particles across the material’s surface. These particles will collect at the flux leakage fields and make them visible to the human eye. Inspectors typically use particles with fluorescent or black coloring to make the defects obvious.
While this is the general process for magnetic particle inspection, you can find more information about testing principles through the International Organization of Standards (ISO) and ASTM International. The guidelines of these regulatory bodies ensure every licensed inspector performs the process effectively.
Types of Magnetic Particle Testing
There are two types of magnetic particle testing procedures — wet and dry. These methods both rely on the same general MPI process where an inspector magnetizes a material to identify defects. The difference occurs in the magnetic particles the inspector applies to make the defects easy to see.
Wet Magnetic Particle Testing
Wet magnetic particle testing (WMPT) applies the particles through a liquid carrier. Inspectors can apply this liquid carrier through a spray or free-flowing liquid. This method allows for quick and even coverage. The liquid also offers long-term mobility for the particles, so they can easily collect at the flux leakage fields for strong defect visibility.
WMPT is ideal for smooth surfaces where the defects are small. On rough surfaces, the small particles in the liquid carrier tend to settle in the surface texture and lose their mobility.
Dry Magnetic Particle Testing
In dry magnetic particle testing (DMPT), an inspector uses a powder to apply magnetic particles to a material. When inspectors apply the magnetic powder, they dust it across the surface to create a thin layer.
Once the powder is applied, the inspector must gently blow off excess powder. This step requires care because the force of air must be strong enough to remove the excess without removing the powder that has settled in the flux leakage field.
DMPT is preferred for rough surfaces like as-cast surfaces and unground welds. It’s also ideal for detecting shallow subsurface defects. Inspectors typically rely on an electromagnetic yoke to apply the magnetic field to the testing material because the AC or half-wave DC current pulses and gives the powder mobility.
Advantages of Magnetic Particle Inspection
Many operations choose magnetic particle inspection because it is:
- Non-destructive: Magnetic particle inspection is a form of non-destructive testing, so your component will be intact following the process. NDT is ideal for pieces you’d like to reference during development or need to continue using before replacement.
- Portable: With the portability of magnetization tools and materials, inspectors can perform MPI anywhere. This advantage is important for components that are too large to ship, and it helps operations save time on delivering their materials to inspection locations.
- Fast: Keeping the timeline moving is a priority for any operation. MPI is a quick process that can deliver results in a short amount of time.
- Easy: The process is relatively easy to master, meaning inspectors across skill levels can learn it and perform it well. It also comes with minimal pre- and post-treatment requirements, like cleaning. These care requirements make it easier for your operation.
- Sensitive: MPI can identify a surface-breaking indication and a near-surface indication. The process can also identify very shallow and fine cracks.
- Flexible: Magnetic particle inspection works with irregular shapes, like components with external spines, connecting rods, crankshafts and other features.
Disadvantages of Magnetic Particle Inspection
While MPI offers a range of benefits, it also comes with disadvantages. Before you opt for MPI, consider the following:
- Material limitations: Magnetic particle inspection only works on ferromagnetic materials like steel, iron, cobalt and nickel. These materials are easily magnetized, allowing the magnetic field to respond to defects. Paramagnetic materials like aluminum will not respond well to MPI.
- Demagnetization: Following the MPI process, components need to be demagnetized to prevent electronic disruption and machining malfunctions. The magnetization can even cause the component to attract abrasive materials that increase wear. The demagnetization process is challenging and may require more skill than the inspection requires.
- Scale: MPI only works well on small sections of material. If you have a large component to inspect, the complete process may take a significant amount of time to complete.
- Depth: It is beneficial that MPI can detect surface and subsurface indications, but its abilities stop there. If you’re looking to identify deeper material flaws, MPI may not be the best route for your quality inspection.
- Paint: While MPI is a form of NDT, testing materials may still be affected. When testing materials have paint layers thicker than about 0.005 inches, the paint needs to be removed. The paint will otherwise interfere with the magnetic field and prevent the inspector from achieving accurate results.
Turn to Fujifilm for Your Non-Destructive Inspection Services
MPI and other NDT methods can be valuable for many operations. Whether you work in automotive, aerospace, biomedical or another critical industry, NDT helps you develop lasting products that operate reliably and keep people safe.
At Fujifilm, our team specializes in a range of NDT techniques to inspect materials and help your operation develop its components. We celebrate innovation and strive to bring valuable services to operations of all sizes and industries. When you turn to our team, you can trust our NDT services to be accurate and align with all relevant industry standards.
Get in touch with us today to learn more about our NDT services.