What Is Predictive Maintenance?
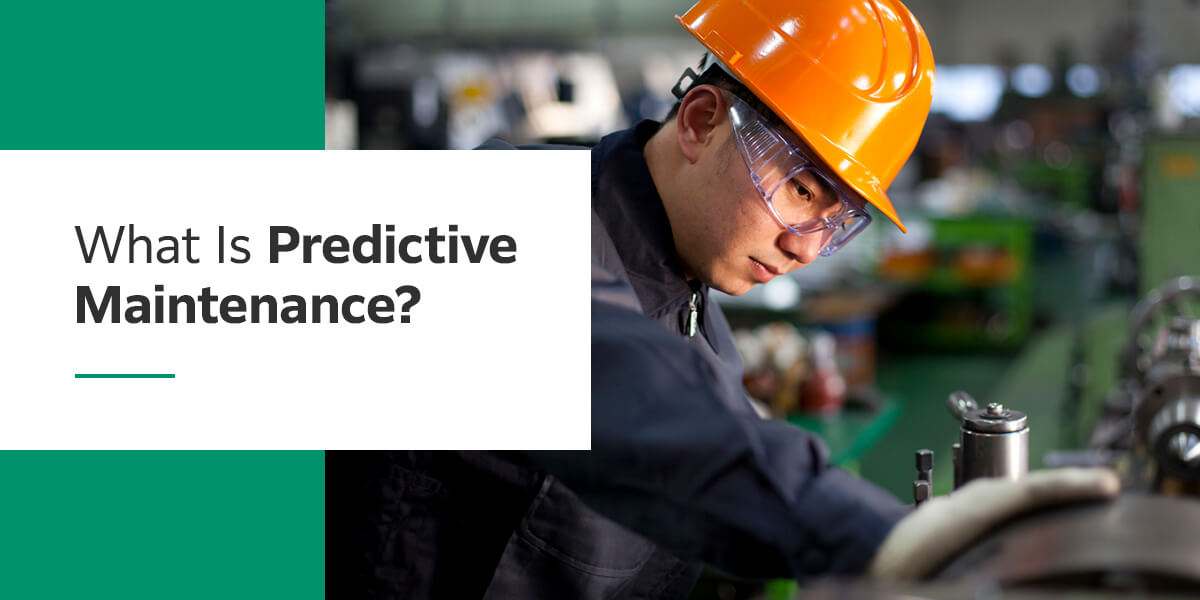
Jump to:
- Types of Predictive Maintenance
- Applications of Predictive Maintenance
- Benefits of Predictive Maintenance
- Predictive Maintenance vs. Preventive Maintenance
- Magnetic Particle Testing Procedure
- Why Choose Us?
- Conduct Non-Destructive Testing With Fujifilm
Predictive maintenance is an advanced technique that allows you to proactively repair your assets before failures occur. It also prevents you from performing maintenance too frequently.
It’s dependent on the Internet of Things (IoT), which is the network of physical objects that connect and exchange data via the Internet. Using advanced technology like Internet-enabled sensors, you can monitor the condition of your assets in real time, which can help you to determine optimal maintenance intervals.
Key Elements of Predictive Maintenance
Other key elements of predictive maintenance include:
- Artificial intelligence (AI)
- Machine learning
- Advanced technology and software
- Integrated systems
- Computerized maintenance management systems (CMMS)
The above tools use non-destructive testing (NDT) methods like sensors and imaging to diagnose imminent failures in their assets. NDT is crucial to this process because it can test a piece or machine without damaging it. This way, you can repair your assets rather than purchasing replacements every time you test them.
Types of Predictive Maintenance
There are several different types of predictive maintenance:
- Vibrational analysis: This is the oldest type of predictive maintenance. It’s most common in manufacturing plants that use high-rotating machinery, and it detects loose parts, imbalances, misalignment and any bearing wear and tear.
- Ultrasonic acoustical analysis: This type of maintenance analyzes a machine’s ultrasonic sounds to detect friction and stress. It’s useful for loud mechanical equipment and electrical devices that tend to be quieter.
- Sonic acoustical analysis: This type of maintenance works for both low-and-high-rotating machinery, but it’s primarily useful for monitoring a machine’s lubrication levels.
- Infrared analysis: Also known as thermographic analysis, this method is practical for a wide variety of assets because it uses temperature to detect abnormalities like cooling and airflow issues. It can even detect abnormal levels of motor stress.
- Oil analysis: This method tests the viscosity, water content and contamination levels of a machine’s oil to determine how worn the equipment is.
- Motor circuit analysis: This technique uses electric signature analysis (ESA) to find irregularities in both AC and DC electric motors. It examines circuitry and circuit components in addition to the voltage and current entering the motor.
One important thing to keep in mind for all types of predictive maintenance is establishing baselines. Before fully implementing a predictive maintenance program, you determine what normal functioning looks like for each of your assets by collecting data from non-destructive tests. Once you’ve completed this step, you’ll have an easier time figuring out whether maintenance is necessary, as readings that are far off the baseline are likely to indicate imminent failure.
Applications of Predictive Maintenance
Matching each type of predictive maintenance to specific assets is key to an effective program. For example, ideal applications for infrared analysis include fluid analysis, electrical systems and discharge patterns.
Here are some common examples of applications for the other types:
- Oil: Hydraulic systems, engines, turbines, transmissions and lubrication levels
- Ultrasonic acoustical: Gas and compressed air leak detection, as well as electrical discharge detection
- Sonic acoustical: Monitoring lubrication levels of machinery
- Vibrational: Imbalance detection, clearances, gear system failures, component alignment testing and resonances
- Motor circuit: Assessing rotor and shaft alignment, engine degradation and insulation
The thing all these applications have in common is that they serve a critical function to an operation. Additionally, each of these applications has a failure mode that regular monitoring can easily predict. These factors should be the most important considerations when deciding whether an asset is suitable for predictive maintenance or another technique.
Benefits of Predictive Maintenance
Predictive maintenance can be expensive upfront due to the high cost of some equipment monitoring techniques. You might also need specialists or other highly trained personnel to make your strategy effective. However, successful predictive maintenance offers many benefits to your operation.
For example, when you implement effective predictive maintenance technology in your operation, you should only need to perform maintenance procedures on assets when necessary — often just before a failure occurs.
Expanding maintenance intervals can benefit your operation in the following ways:
- Save money: By performing maintenance only before failures, you don’t have to purchase parts and supplies as often as you would using other maintenance techniques. Studies suggest that an effective predictive maintenance strategy can save an operation as much as 8%–12% more than a program that prioritizes preventive maintenance.
- Minimize downtime: Of course, predictive maintenance will prevent unexpected downtime from occurring. But it’s also worth mentioning that you’ll have less downtime as well by reducing the amount of time you need to spend actively performing maintenance on your assets.
- Decrease breakdowns: Monitoring your assets in real-time alerts you to imminent failures before they happen, so you’ll be able to keep unexpected machine failures to a minimum, thus increasing productivity and maximizing uptime.
- Improve safety: By preventing unexpected breakdowns and failures, you can protect your technicians and operators from accidental injuries.
It’s important to mention that predictive maintenance strategies may not be effective for every asset in your operation. To determine whether a piece of equipment is suitable for this strategy, you can use reliability-centered maintenance (RCM) techniques.
RCM can help you identify your operation’s most critical assets — those likely to experience frequent failures or those that would affect your operation the most in the event of a failure. These critical assets are the ones to which you should apply your predictive maintenance strategy.
Predictive Maintenance vs. Preventive Maintenance
Preventive maintenance is another popular maintenance technique across many industrial applications. It involves performing regular maintenance before an asset experiences problems that result in failure.
While the two may seem similar, there are two key differences between predictive and preventive maintenance:
- The data you will analyze
- The timeline of that data
Predictive maintenance relies on real time measurements to determine an asset’s condition. The IoT sensors on the asset gather this information. By comparing this data against the asset’s baseline, you can easily determine whether maintenance is needed at this time.
On the other hand, preventive maintenance uses historical data, like averages and life expectancy statistics, to predict when the asset might need maintenance. While there is proof that preventive maintenance reduces asset downtime and improves efficiency, predictive maintenance procedures are more accurate at predicting the precise moment when repairs are necessary.
Magnetic Particle Testing Procedure
Magnetic particle testing (MPT) is a cost-effective NDT method commonly used in predictive maintenance. It uses a magnetizing force or magnetic field for assets made of ferromagnetic metals to detect surface and shallow subsurface flaws. You can either magnetize the object or spread metal particles on the object. Use cases for this process include aerospace and oil and gas companies that must radiographically inspect parts.
How Does MPI Testing Work?
To perform a magnetic particle inspection (MPI), you will need to follow five steps, including:
- Pre-cleaning
- Magnetization
- Application of magnetic particles
- Inspection
- Post-cleaning
The magnetic particle inspection procedure is a combination of two NDT methods — magnetic flux leakage and visual testing. Demagnetization in magnetic particle testing is a critical step, especially for sensitive equipment or components. There are two types of MPI — dry magnetic particle testing (DMPT) and wet magnetic particle testing (WMPT).
Why Choose Us?
At FUJIFILM North America Corporation, we understand the critical role predictive maintenance plays in ensuring operational efficiency, safety and compliance. With decades of expertise in industrial imaging and a commitment to innovation, we provide solutions designed to empower you.
We develop software in-house and offer troubleshooting for NDT equipment across the United States. Our personalized customer service, expertise and streamlined inspection process mean our solutions will easily integrate into your workflows, offering flexibility and scalability to meet your specific industry requirements.
Our innovative imaging systems go beyond defect detection, providing actionable insights that help you predict and prevent failures before they happen. We build our radiographic solutions to withstand demanding environments while maintaining accuracy and consistency to maximize customer value.
Conduct Non-Destructive Testing With Fujifilm
As a pioneer of the imaging products industry for decades, you can trust us to deliver innovative solutions for your operation. We provide superior non-destructive testing systems using digital radiography and conventional X-ray imaging.
Are you looking to push your workforce to another level? We also offer comprehensive NDT training courses in digital radiography to prepare learners for certification. Your staff can learn from expert instructors either through regional classes or on-site in your facility.
Contact us to learn more about how Fujifilm’s non-destructive testing options can benefit your operation.