Why Assisted Defect Recognition is Necessary in NDT
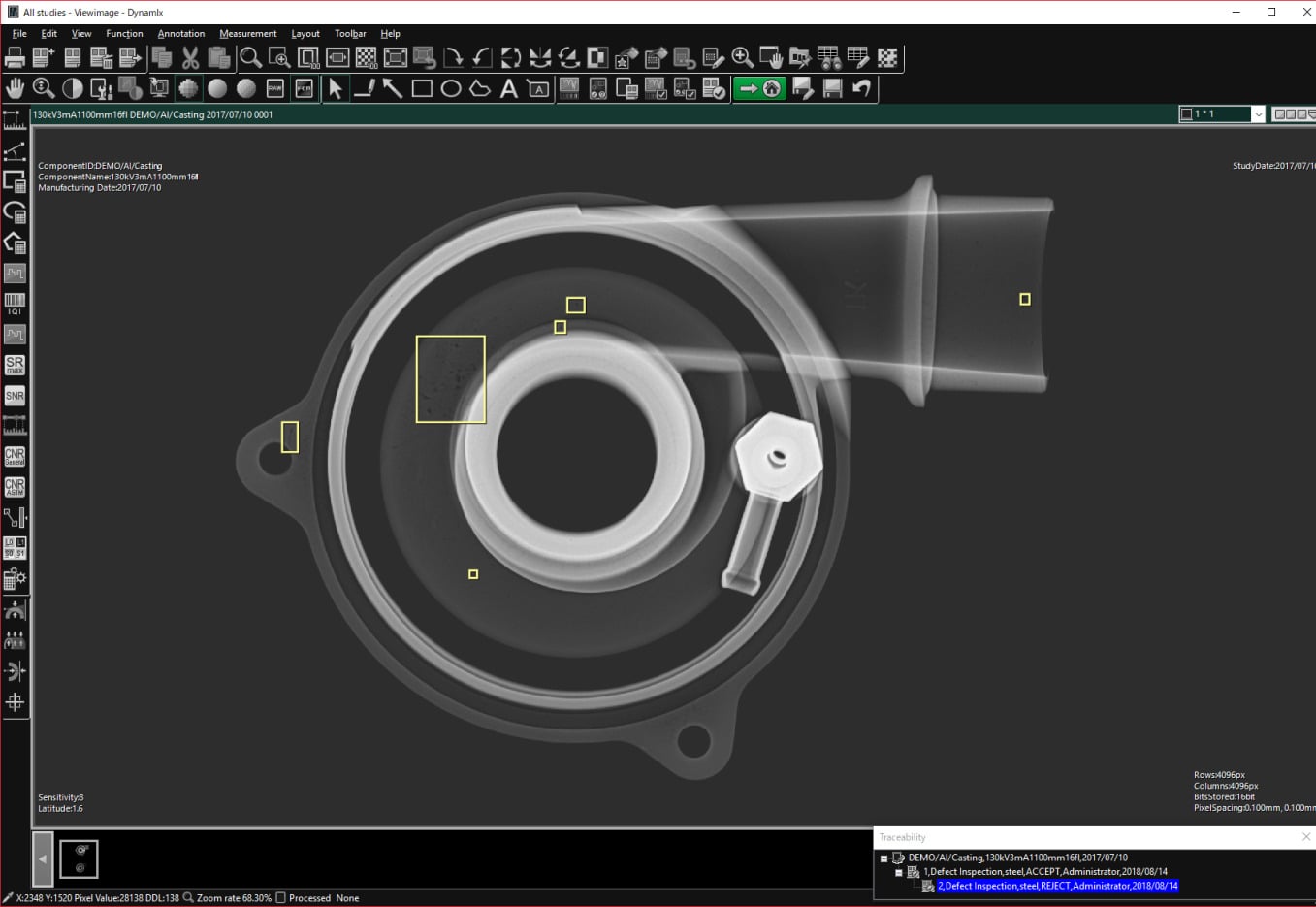
Jump to:
Assisted Defect Recognition (ADR) software is crucial to any company that wants to perform highly accurate non-destructive testing (NDT). Many companies across a wide array of industries use ADR to test their parts and ensure they’re defect-free, whether these parts are rolling off the assembly line or are already installed in machinery. By learning about ADR and using it at your company, you can reap several benefits that can set you apart from the competition.
Find out more about what ADR is, why it’s needed and some of its primary applications by reading below.
What Is ADR?
ADR is a type of software designed to help companies know whether they should reject or accept new parts. When people use ADR, they’ll send images of a part into an inspection software system. This system then processes the images and helps users spot potential defects. With this method, the user sees possible errors on their computer screen and marks them manually. The information ADR provides to the user helps companies make more informed decisions about rejecting or accepting various parts.
Sometimes, people also refer to automatic defect recognition as ADR, creating some confusion with the acronym. Essentially, automatic defect recognition is a more advanced form of ADR where AI software automatically detects defects. Besides checking for defects, it also decides whether to pass or fail a part based on various programmed specifications, such as the number of flaws or a flaw’s size. This type of software makes the process faster and reduces the time staff members spend evaluating a part.
However, while automatic defect recognition is a revolutionary new technology, it’s still in development, and companies aren’t ready to use a fully automated solution due to various regulations. Therefore, ADR is more widely used, with parts of it featuring automation and the ability to detect defects. For example, ADR software can highlight defects, such as scratches, cracks, shape errors and bumps, to help operators more easily find issues and make a decision.
Why Is ADR Needed?
ADR is essential since it allows companies to document test results in a reliable and repeatable manner. Since ADR utilizes software, companies can test parts electronically which minimizes the risk of human inspection errors. When you use ADR correctly, you reduce the chances your inspectors accidentally reject parts that work correctly or pass parts with significant defects. As a result, you can increase customer satisfaction and lower costs associated with rejecting parts in error.
Alongside ensuring you’re passing and rejecting the right parts, ADR is essential for parts that could impact machinery’s safety or proper functioning. Since ADR gives you greater accuracy and can spot defects, you’ll be more likely to spot mistakes that could cause adverse consequences. By spotting these errors, you can better prevent injuries to operators and damage to machinery or other complex systems.
Additionally, ADR is crucial for companies working on a tight deadline. Having to manually document and test parts for defects can take a lot of time. When you use ADR systems and software, you speed up the process significantly, helping you reach your goals and increase your output. Besides improving your speed, ADR systems help you spot statistical trends to understand where you need improvements.
Industry Applications for ADR Software
Since ADR is crucial for testing parts and components, companies use it for various industrial applications. For example, many companies use it alongside their NDT procedures. Due to ADR software’s ability to detect defects without harming the part being tested, it’s an excellent way for companies in industries that rely on safe in-depth testing for their products, components and systems.
You can often find ADR software used in the oil and gas industry to ensure oil rigs and pipelines don’t have any defects. You can also see companies in the energy industry relying on ADR software for testing complex parts in nuclear and thermal power plants. Additionally, transportation industry companies use ADR software to ensure aviation or railway parts meet regulations and quality standards.
The manufacturing sector is another major industry relying on ADR software. Manufacturers often have to create diverse materials, from automobile parts to consumer products, that make reliability and functionality a primary goal. ADR software allows these companies to ensure they meet consumer expectations by delivering exceptional products. While all of the industries above rely on ADR software, you can also find this software used in other industries needing to check the surface of various materials, such as ceramics, textiles and metals.
Benefits of ADR
More companies are turning to ADR software for the many advantages it gives them. Find out more about the primary benefits of ADR software below:
- Reduce personnel cost: When you use ADR, you can automate some essential testing procedures. Since ADR allows companies to quickly test a part or system’s imperfections and only requires the operator to make a decision, you can reduce personnel costs. By taking away the need for manual inspections from staff members, you can reduce the number of personnel you need to conduct inspections. As a result, you can reduce expenses related to paying personnel to perform inspections.
- Lower chance of human error during the inspection process: Even the best inspectors can miss defects in a part. ADR software safeguards your company from human error during the inspection process by automating much of it. Since ADR software delivers more reliable and consistent evaluations, you take away some of the risk of human variability in the inspection process.
- Improve quality control: If you produce or utilize parts requiring NDT in your operations, you’ll likely want them all to provide a high level of quality for a long time. Using ADR can improve your company’s quality control efforts by reducing the risk of human error and tracking your parts over the long term. Due to ADR software’s ability to document your inspections and keep details about them in your system, you can quickly spot trends and make corrections to processes that tend to produce more errors.
- Faster cycle times: Since ADR helps you automate at least part of the inspection process, you can produce new parts faster. ADR allows you to have shorter cycle times, as it removes the need for manual inspections that tend to take longer than those done by ADR software. By getting parts to market faster, you can potentially raise your profits by producing more sellable products.
Choose Fujifilm for Your NDT Needs
At Fujifilm, we excel at helping companies transition to Industry 4.0. As you look to automate key NDT tasks, reduce costs and increase your efficiency, let us help. We can provide you with several NDT products you can rely on to streamline your inspection processes, making them faster and more accurate. Additionally, you might be interested in pairing our NDT products with our Dynamix VU imaging software, as it provides the highest level of image process technology for today’s rigorous testing standards.
If you’re interested in our NDT services and ADR software, take a moment to contact us to schedule a demo of our current ADR software. Minor adjustments may be necessary based on part requirements and configuration.