Pressure Change Testing
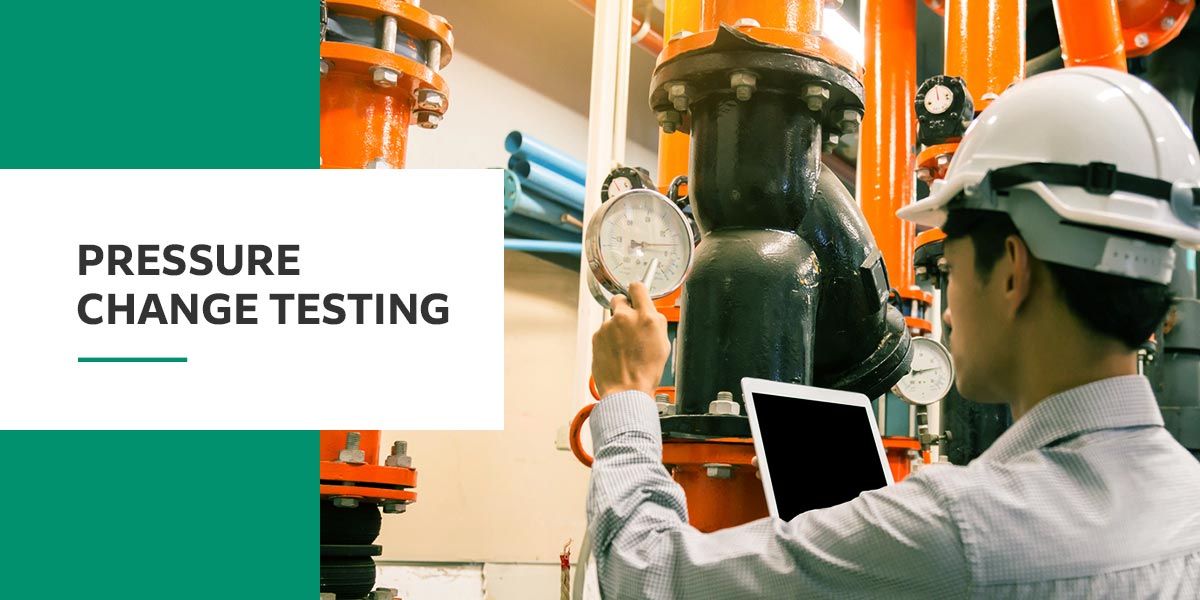
Jump to:
- What Is Pressure Change Testing?
- How Does Pressure Change Testing Work?
- What Is Pressure Change Testing Used For?
- What Are the Benefits of Pressure Change Testing?
If you work with pressure equipment — building it or using it — you’ll need a reliable testing method. Testing is vital to keeping people and employees safe and is often required by various entities, like insurance companies and government organizations. One way to test your equipment’s pressure and look for leaks is through pressure change testing. This procedure is fast and accurate, making it a helpful way to investigate the condition of your equipment without time-consuming or expensive processes.
What Is Pressure Change Testing?
Pressure change testing is a method of non-destructive testing (NDT) that assesses the integrity of a pressure shell. It’s typically used on new equipment or equipment that has recently been repaired or modified, but it’s also appropriate for periodic testing. Another possible application is to use it to determine a pressure rating when calculations are inadequate. Manufacturers commonly use this versatile testing method to test equipment before it reaches the customer, and many other businesses use it to keep pressure systems in good condition.
The NDT pressure testing process involves monitoring the change in pressure over time and determines the allowable leakage rate for a closed component system or a system that requires a specific pressure or volume.
How Does Pressure Change Testing Work?
Several different kinds of NDT pressure change testing exist, with some of the most common being hydrostatic, pneumatic and vacuum testing. All are based on similar principles, with the medium being used to add pressure changing. In pneumatic testing, for example, the vessel being tested is filled with air to a specified pressure. Then, the air source is cut, and any change in pressure is measured.
The general pressure decay testing process looks like this:
- The tester attaches the part to a test port and opens one valve to increase the pressure within the part. Once the pressure reaches a specific value, the second valve is closed. Shortly after, the first valve is closed, allowing the line between the valves to vent out through the first valve.
- The part is left alone for a short period, with the duration depending on the testing standards and part size. The testing equipment detects any pressure that escapes through the second valve. If this measurement exceeds the specified tolerance, the part fails the test, and the testing equipment should display the reason for the leak and the amount.
- When the test is finished, the pressure trapped in the part can be vented.
The testing equipment used and the part size will affect the process, but this procedure is quick and simple for most parts.
What Is Pressure Change Testing Used For?
The high energy concentrations stored in pressure equipment can easily create safety hazards for the general public and employees if released unexpectedly. Of course, the effects can also affect downtime and business operations. Even if no modifications occur, failures in pressure equipment can come from many places, like aging, wear and tear and manufacturer defects. Checking for failures is necessary for everyday operation and manufacturer quality testing.
Several different entities use pressure change testing in their requirements or guidelines, including:
- The United States Department of Energy (DOE).
- The United States Department of Transportation (DOT)
- The Occupational Safety and Health Administration (OSHA).
- The American Society of Mechanical Engineers (ASME).
- Other local and state organizations or codes.
- Terms of contract for construction work.
- Insurance providers.
Many of these organizations turn to ASME codes, such as ASME B31 Pressure Piping Code and ASME Boiler and Pressure Vessel Code. They might require testing at specific intervals or during audits. You’ll need to stay compliant to avoid hefty fines. Testing can also help you ensure your equipment is in good shape and isn’t deteriorating or that it reaches your customers in pristine condition. More importantly, pressure change testing is critical to creating a safe environment for employees and the general public.
A strong pressure testing program can detect problems before they cause complete failure. Testing processes can also help you determine whether you need to adjust the typical operating pressure of the vessel or make changes to keep it running smoothly at the desired pressure.
Another way to use pressure testing is to establish pressure ratings for components or systems where calculations are insufficient. In this process, the pressure is gradually increased in a prototype part until measurable results appear or the part ruptures. Derating factors pulled from the standards can help establish the designated pressure.
What Are the Benefits of Pressure Change Testing?
Testing your pressure equipment is critical, but what makes pressure change testing a good method? It has several advantages over other types of testing:
- Sensitivity: Although sensitivity depends on the size of the part and the time spent on the test, pressure change testing is generally sensitive enough to detect even small leaks in the equipment.
- Speed: While large parts may require more time, many tests can be completed in minutes, making it an efficient step in quality assurance processes and regular testing programs. User-friendly testing equipment can make it even faster by simplifying the process for testers.
- Versatility: Pressure change testing can use various mediums, so you can test in pressurized or vacuum environments and determine leak rates with this method. You also get various configuration and reporting options, including measurements assessing pressure or flow loss.
- Non-destructive: As a type of NDT pressure testing, pressure decay leak tests don’t damage the part. This makes them ideal for quality assurance processes and regular testing demands. You can test the part and maintain thorough documentation of it before sending it on to the customer or putting it back into service.
- Widely accepted: With the ASME standards, pressure decay testing is a highly standardized, accepted method that delivers data that various organizations can understand.
Pressure change testing is useful for preventative monitoring programs or for applications like high-volume quality testing. It’s quick, effective and popular. However, like any testing method, you’ll need the right equipment if you want reliable results.
Explore Non-Destructive Testing Solutions at Fujifilm
At Fujifilm, we offer a wide range of NDT solutions. We build equipment for a wide range of customers, including partners in highly regulated industries like aerospace and medicine. Along with reliable testing equipment, we’ll ensure your team knows how to use it well with thorough training from experienced representatives.
Reach out to us today to learn more about how our NDT solutions can support your operations.