How Is NDT Used in the Electronics Industry?
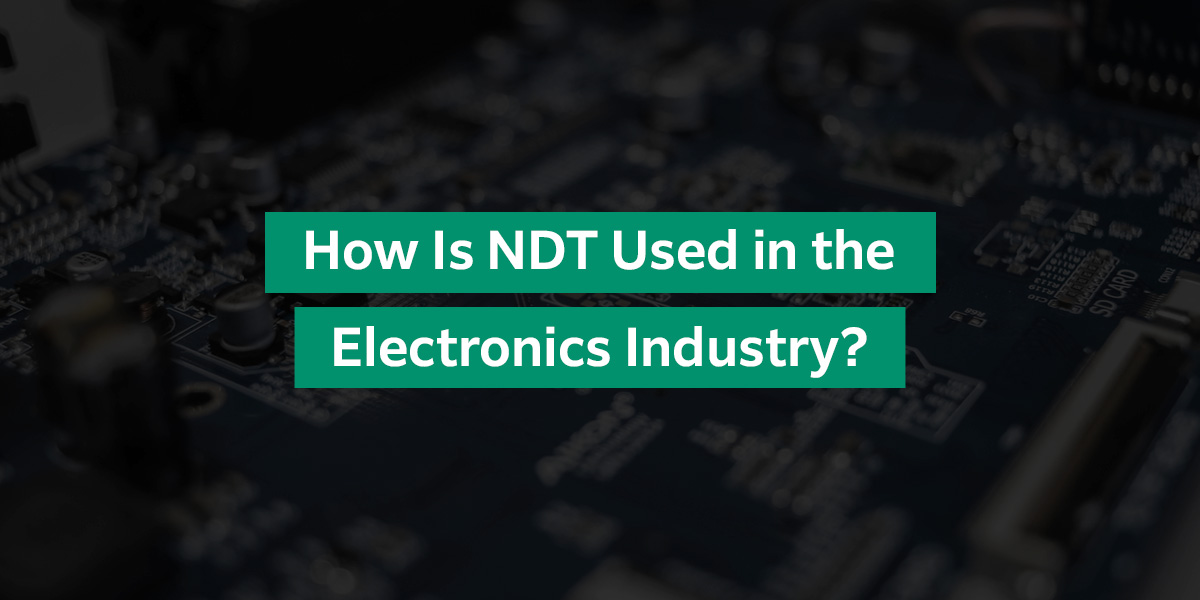
Non-destructive testing (NDT) is used in several applications in the electronics industry. The field is highly competitive, with strict quality demands and the need for speedy production processes. NDT refines the quality control process, ensuring products are functional and interior structures are in good condition before going out to the customer.
Common Defects Within the Electronics Industry
Electronic components form the backbone of technological products. Defects can drastically affect functioning and alter an item’s usability. They’re usually caused by discontinuities or out-of-spec constitutions. Even the most rigorous quality control measures can let some faults slide.
Non-destructive testing typically uses diagnostic imaging software to identify defects where quality control measures may miss them. It can also play a role in pinpointing the following common defects:
Soldering Defects
Wave soldering attaches electronic components to a printed circuit board (PCB) to create a functioning electronic assembly. This process gets its name from using molten solder waves to attach the metal components of the PCB.
In reality, wave soldering is more of a waterfall than a wave. The PCB components are loaded onto the board, which passes under a waterfall of solder held by a set tank size. A protective coating is placed over circuits that don’t require soldering, which produces a reliable electrical connection. The solder only wets the exposed areas of the circuit board, which prevents electrical errors.
Wave soldering is generally a better option for large-scale soldering processes as it’s quick and produces high-quality PCBs. However, it isn’t perfect, and there is room for error. With surface-mount PCBs, the electrical components are first glued in place before workers run them through a solder wave. This step, as well as manual soldering, can lead to potential human error faults.
Wave soldering becomes more difficult as the pitch decreases. Generally, the ideal minimum pitch is somewhere around 0.5mm. You can use shorter lead lengths or add solder thief pads to the circuit artwork, but there’s still a chance of fault. That’s where non-destructive testing like digital detector array (DDA) equipment comes in. It can help you detect these common soldering defects:
- Bulbous joint
- Cracked joint
- Flux residues
- Incomplete joint
- Lifted pads
- Pad contamination
- Poor wetting
- Solder skip
Component Shifts
Component shifts commonly occur when mismatched parts are attached to the pad, which sections the part towards its nearest thermal mass. The fault usually begins in the reflow stage. Other causes of component shifts are heat sinking, oxidation and bent leads.
Humidity and temperature control are two significant factors to monitor to prevent component shifts. High humidity and temperature can cause the component to oxidize, which could result in it shifting. Electronic component NDT can help identify component shift errors like bent leads, and you can fix them at the manufacturing level to prevent faulty products from going out to customers.
Try to reduce the number of movement components and monitor reflow profiles like temperature and humidity. To take it a step further, use aggressive flux to boost the solderability of the PCB and prevent defects like bent leads.
Wire Bond Quality
NDT is frequently used in the electronics industry to spot wire bond errors. It’s a promising technique for defect detection, and it can prevent failure modes. Faults can affect your chances of meeting MIL-STDs and result in product wastage and unnecessary business expenses.
- Cratering bond wires: Wire bonding uses thermocompression, which involves high heat and intense pressure. This process can cause cratering and peeling of the wire bond. Over time, the product will show performance issues when handling high-speed signals. It could result in complete disconnection.
- Contorted bond wires: The pressure during manufacturing can cause the bond wires to overstretch, bend or twist. Bond wires are typically hardened to improve signal retention, speed and consistency. However, their hardness also makes them brittle and prone to breakage. When contorted beyond their specs, they can cause the board to fail, especially when exposed to high temperatures.
- Untamed bond wire tails: It’s important to cut the wire bonds on each end cleanly. If not, the tail can extend onto another pad or wire and increase the capacitance of that bond. It causes shorting, cross-coupling and increased parasitic inductance, which could affect the functionality and performance of the PCB.
- Insufficient mechanical adhesion: NDT is commonly used to test the adhesion of electrical connections. Weak bonds can cause capacitances and incur more resistance than a product’s board is meant to handle. The increased resistance causes localized heating, weakening nearby bonds and leading to complete failure of the circuits.
How Is NDT Used to Detect Defects in the Electronics Industry?
Using NDT for electronics helps examine the internal structures of electronic components without causing damage to the item. There are different types of NDT methods, like thermography and radiography. They can test various electronic components to ensure a functioning product. Some of the common defects they can identify are:
- Component shifts
- Connector faults
- Integrated circuits
- Pad contamination
- Soldier joint faults
While visual inspection can help identify some faults, NDT analyzes through layers of materials. Using NDT, inspectors can identify connection issues that alternatives can’t. It also saves a lot of time by helping technicians pinpoint the root cause with ease. In industries like additive manufacturing (AM), where the process is highly complex, NDT optimizes quality control and helps meet strict functional requirements.
NDT also helps technicians detect subtle manufacturing defects that aren’t easily identifiable using conventional methods. Over time, these minuscule faults can affect the functionality of the circuit and lead to failure and connectivity issues. These non-destructive techniques, like X-ray inspection, effectively check for damage. They enhance the mechanical properties of important electrical components that play a key role in industries like aerospace, nuclear and energy.
How Can Computed Radiography and Digital Radiography Help?
Radiographic testing (RT) is a testing method that uses X-ray software or gamma rays to analyze the internal structure of electronic components. It helps identify faults or defects in manufactured electrical items.
X-ray inspection uses electromagnetic radiation to penetrate objects. It allows you to attain a high level of detail about the internal structure without opening or damaging the items.
To perform an X-ray inspection for electronics, place the test board or part between the radiation source and film. The differences in material density and thickness will lower the radiation that penetrates the part, revealing any differences in absorption throughout the board. The results reveal a visual recording of potential faulty areas or heat sinking.
X-ray NDT methods provide an added layer of quality assurance. They point out defects that can’t be seen with the naked eye or conventional testing methods.