What are NDT Discontinuities?
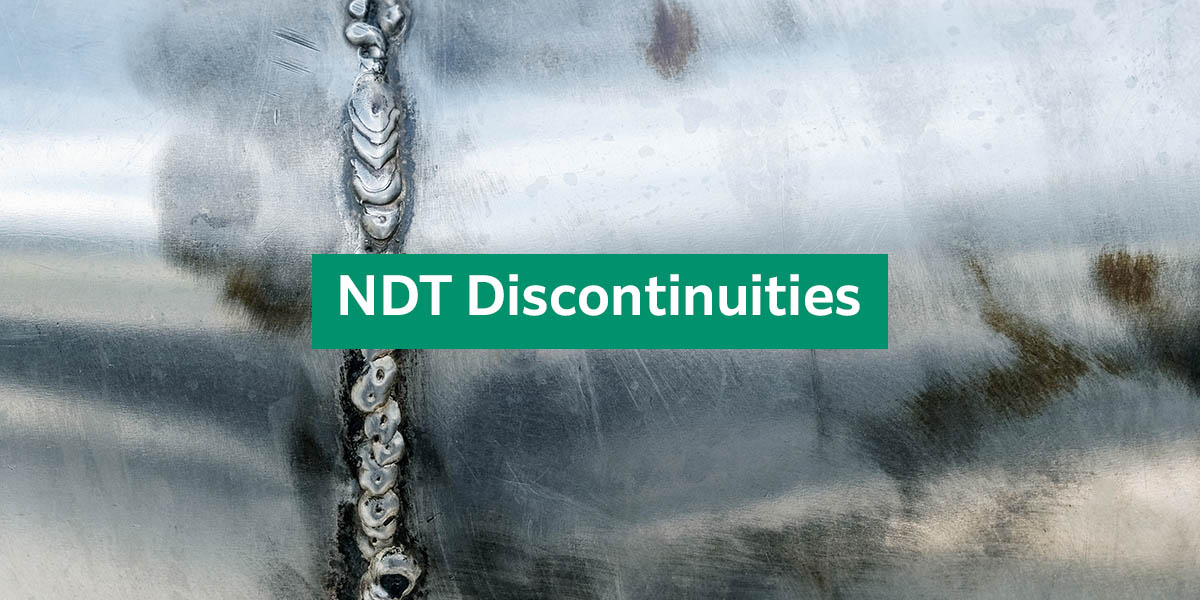
Discontinuities are common in the manufacturing industry and are part of quality control measures. Non-destructive testing (NDT) methods like radiography and visual inspections identify and characterize critical characteristics in materials or components to maintain safety standards.
Identifying and categorizing discontinuities in the aerospace, construction, engineering and manufacturing industries ensures reliability and safety. NDT is a vital technique that helps with quality control and risk mitigation to ensure the longevity and performance of materials and components across these industries.
What Is the Definition of NDT Discontinuity?
In non-destructive testing, a discontinuity is any interruption or irregularity in a material that can affect the component’s performance or properties. NDT processes evaluate and identify various forms of discontinuities to verify the integrity and quality of a component or material without damaging it. They also detect dimensional discrepancies, such as deviations from specific dimensions, improper component assembly and thickness variations.
What Are the Types of NDT Discontinuities?
NDT detects various types of discontinuities that form for several reasons. Technicians divide these origins into three categories:
- Inherent discontinuities: When metal is molten during casting, its malleable trait can lead to wrought discontinuities. These often come from the ingot’s melting and solidification before it forms into billets, blooms or slabs. Inherent cast discontinuities come from melting, casting and solidification.
- Processing discontinuities: Processing discontinuities occur during the manufacturing process. Some examples include heat treating, welding, rolling, machining and plating.
- Service discontinuities: Corrosion, erosion, fatigue and stress occur during everyday use during a material’s service life. Service discontinuities change stress distribution, which affects the material’s expected service conditions. These discontinuities can also impact chemical or mechanical properties, like corrosion resistance.
The multitude of types of discontinuities that may form internally, on the surface or in the subsurface of a material. These include:
- Cracks: Cracks appear as fractures or fissures in the material that are surface-breaking or internal. They can result from fatigue, manufacturing flaws or stress to the material or component.
- Inclusions: Inclusions are foreign materials that weaken a material’s properties. They can include oxides, non-metallic particles or slag that get trapped in the material during processing or manufacturing.
- Porosity: When gas gets trapped during solidification, material impurities or improper welding techniques, small cavities or voids form in the material, causing porosity.
- Voids: Voids are similar to porosity, but these empty spaces in the material are bigger and more noticeable. They affect the mechanical properties and structural integrity of components.
- Weld imperfections: Discontinuities in weld joints, such as lack of fusion, undercutting, weld porosity or incomplete penetration, compromise a welded structure’s strength and reliability.
- Laminations: Parallel discontinuities or laminations sit between the layers of a composite material or laminated structure. These occur from delamination during service conditions or manufacturing.
- Surface irregularities: Surface imperfections like corrosion, dents, pits or scratches affect a material’s appearance, functionality and integrity.
NDT discontinuities are also categorized according to their orientation and shape within materials. The categories include:
- Linear discontinuities: These flaws have a linear shape and can be surface-breaking or internal. Examples include laps and lack-of-fusion faults in welds and seams. Ultrasonic testing (UT), eddy current testing (ECT) and magnetic particle testing (MPT) can effectively detect these irregularities.
- Plantar discontinuities: Plantar discontinuities have flat surfaces within or on the surface of a material. Delaminations, laminations and parallel cracks are part of this classification, detected by UT, radiographic testing (RT) or visual inspection.
- Volumetric discontinuities: These irregularities extend through the volume or thickness of a material with little to no surface features. RT, UT, computed tomography or magnetic flux leakage can detect and assess these discontinuities.
What Is the Difference Between a Discontinuity and a Defect?
While all defects are discontinuities, not every discontinuity is considered a defect in NDT. The main reason is that NDT identifies and distinguishes between harmless discontinuities and defects that are critical to material reliability, quality and safety.
Discontinuity | Defect | |
Definition | The definition of a discontinuity in NDT is an interruption or deviation in a material’s structure or composition. They vary in shape, size, orientation and location in a material. | In NDT, a defect refers to a flaw that exceeds acceptable standards for the intended application. Defects are significant enough to potentially compromise the material’s functionality, strength or safety. |
Types | They can include cracks, inclusions, porosity, lamination or voids in a material’s properties. | Defects’ classification depends on their location, orientation, shape and size. |
Nature | Discontinuities may or may not be detrimental to a material’s performance. | NDT inspections assess whether discontinuities are defects according to quality criteria. |
Detection | NDT techniques identify and evaluate discontinuities without damaging a component or material. | After a defect is identified, further evaluation and characterization determines whether corrective action is necessary. |
How Is NDT Used to Detect Discontinuities?
Various NDT methods detect discontinuities based on factors like defect size, depth, accessibility and orientation. Techniques often used include:
- Radiographic testing: RT uses X-rays or gamma rays to create a radiographic image on film or digital detectors to visualize cracks, voids or inclusions.
- Liquid penetrant testing: Capillary action detects surface-breaking defects in non-porous materials. After a dwell time, the excess penetrant is removed and a developer draws out penetrant from surface defects by increasing their visibility. This technique helps to inspect forgings, castings and welds or machined components made of ceramics, metals or plastics.
- Eddy current testing: ECT uses electromagnetic induction to pickup on surface or subsurface defects, material thickness measurements or conductivity variations. These discontinuities, which include cracks and corrosion cause changes in the eddy currents.
- Magnetic particle testing: Using magnetic fields and particles, this technique detects defects in ferromagnetic materials. The magnetic particles accumulate in areas of magnetic flux leakage caused by cracks, laps or seams in welds, forgings or castings.
Find NDT Solutions With Fujifilm
NDT technicians can identify and characterize discontinuities using various techniques. The information they gain from these tests allows them to determine whether corrective action is needed to amend safety or material quality control.
Thanks to decades of expertise, Fujifilm offers superior NDT image quality. As a leader in NDT imaging technologies, we help clients in many industries with cost-effective solutions that offer flexibility, quality and speed. These include our durable, high-res DDA systems and the Dynamlx HR2 CR system. Contact us today to learn more about our various NDT solutions or a service request.