How Is NDT Used to Inspect Welds?
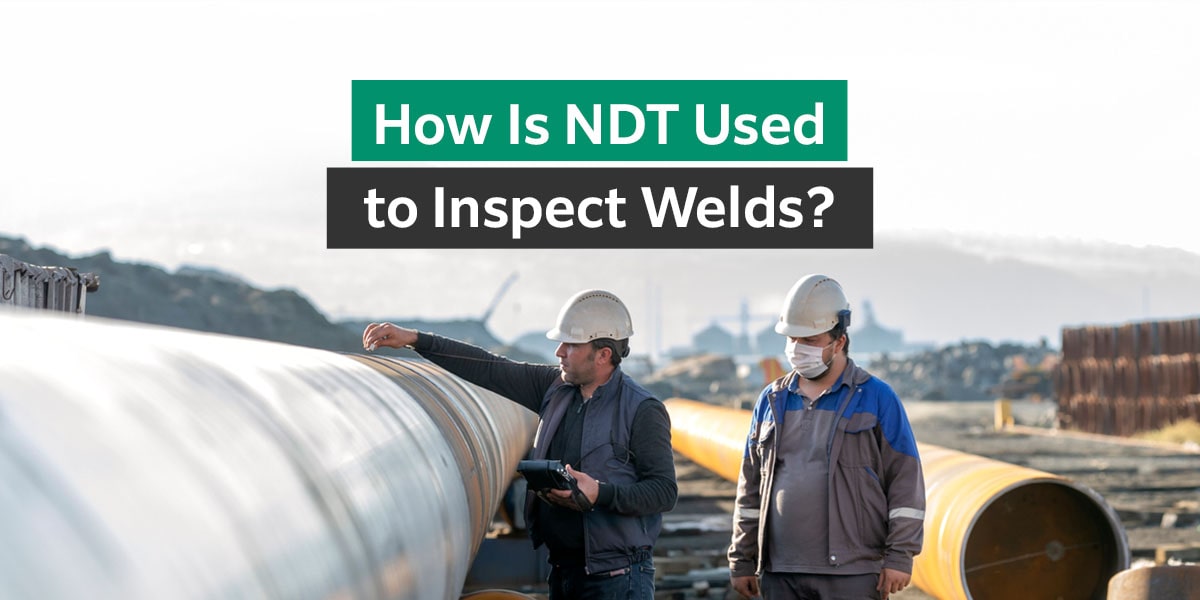
Jump to:
- Understanding Weld Inspection
- Types of X-Ray Equipment Used for Weld Inspection
- Industries & Applications for Weld Inspection
- How NDT Supports Weld Quality Assurance
Welded joints are responsible for crucial structures and components in many different industries. To ensure the welds maintain their quality and integrity, they must undergo inspection with a method that won’t impact performance. Non-destructive testing (NDT) offers this kind of inspection with fast, precise and affordable technology.
Common NDT methods include traditional and digital radiography, which come in several forms and can be selected for different applications and operational requirements. They facilitate better quality assurance on a weld without damaging it. Matching the right NDT technology to the weld and the environment can make a significant difference in the efficacy of the scan and its benefits to a specific workflow.
Understanding NDT for Weld Inspection
NDT is a broad category, but its defining feature is that it does not damage the scanned object. It can stay in service and continue doing its job after the test. A destructive test, in comparison, might involve breaking open a part to inspect the material’s structure or applying heavy weight to see how it responds. For example, a manufacturing facility could perform spot tests by randomly selecting a part and breaking it open to assess its internal structure.
By avoiding damage and subsequent replacements, NDT can help save time and money on assessments. While there are many NDT testing techniques, some common ones include radiographic, visual, leak and acoustic emission testing. Strategies like these can help confirm the completeness of the weld, its location, coverage and other characteristics, ensuring compliance with codes and safety requirements.
Since welds typically need to remain undisturbed, NDT is ideal for confirming quality, especially in critical applications like large infrastructure or aviation equipment. Welds can be exposed to various forces, like vibrations and pressure, during regular operation, and NDT allows for easy, regular inspections. It also provides a convenient way to monitor defects that could become more significant problems, such as a crack that is only concerning if it grows.
Some of the issues in welds that NDT might look for include:
- Excessive or inadequate weld reinforcement
- Cold lap
- Cracks
- Internal concavity
- Cluster porosity
- Incomplete fusion
- Slag inclusions
- Internal or external undercuts
If NDT catches any defects, they can be fixed to prevent costly consequences. If the weld meets expectations, the permanent record gets filed away and stored safely for compliance. The company has a full, unbiased image of the weld’s quality.
What Types of X-Ray Equipment Are Used in Weld Inspection?
Radiography is a valuable type of NDT that creates images based on how an object absorbs radioactive waves. As with the field of photography, digital tools have changed the way we process X-ray films. Now, you can choose your X-ray welding test method from film radiography, which uses traditional techniques, and digital radiography, which collects images digitally for easier storage and management.
1. Traditional Film Radiography
A weld X-ray taken with traditional film creates a latent image on the film. When the film is exposed to radioactive waves from the X-ray equipment, radiation-sensitive silver halide crystals in the inner layer rearrange themselves. When an object blocks the radiation, those waves won’t hit the crystals and cause them to react, leaving the image of the object. The X-ray film processing phase is similar to a darkroom for photography and makes the film’s image visible.
Companies using traditional film must consider its unique storage and processing requirements and the consumable materials needed to process it. These films are sensitive to humidity and light, and they can take up considerable space.
2. Computed Radiography (CR)
Computed radiography (CR) is a type of digital radiography. Instead of film, it relies on reusable imaging plates with a phosphor that responds to radiation. The process looks similar to that of traditional film but with the imaging plates behind the object instead of film. After the image is taken, a CR reader scans the plate and digitizes it for viewing on a workstation. Digital radiography can benefit from diagnostic imaging software that helps improve image quality, assist in analysis and streamline file management.
Without the need for consumable materials or sensitive storage requirements, CR is much simpler and more affordable than film. Some CR software also provides advanced tools that can drastically improve inspections.
3. Digital Detector Arrays (DDA)
As another digital radiography tool, digital detector array (DDA) technology can produce instant scans using a DDA panel. These panels — with the help of software — develop the image with little processing time and provide high-resolution results. A significant advantage of DDA technology is its immediate results. While CR would require processing with a large CR reader, usually kept in a stationary setting like an office, DDA panels can immediately provide images in remote locations.
Weld Testing Industries and Applications
X-ray weld testing provides insights into weld quality across many different fields and applications, especially those with strict compliance requirements. NDT methods may be required to collect permanent records that demonstrate the quality and safety of a structure or product.
Some of the industries that rely on NDT include:
- Aerospace
- Automotive
- Engineering and infrastructure
- Military
- Construction
- Maritime
- Oil and gas
Most companies find that a certain type of testing works better for their application than others. For instance, a business that needs in-field testing might opt for DDA panels, which can provide portable inspections in normal lighting conditions. An organization that needs to conduct pipe weld X-ray inspection might choose Computed Radiography because its image plates can wrap around pipes and other rounded objects.
How NDT Supports Weld Quality Assurance
NDT is ideal for quality assurance in welding. You can use it on new welds or welds that have been used for some time. By identifying defects and inconsistencies, NDT allows you to evaluate a weld joint’s integrity and strength without impacting it. Alongside watching for defects, NDT can also help with precise assessments of weld geometry and dimensional exactness once the weld is in place. It offers convenience, accuracy and speed.
NDT, particularly radiography, provides reliable, permanent inspection records, which many companies need for compliance and internal quality assurance processes. As a versatile testing method, NDT can accommodate many types of structures and workflows.
Fujifilm’s NDT Solutions for Welding Inspections
When you need to conduct reliable, accurate and convenient NDT processes, trust the industry leaders. Fujifilm has a long history of supporting quality assurance processes across industries and applications with our digital and traditional radiography equipment. We offer sophisticated hardware, diagnostic software and consumables like traditional X-ray film and developing chemicals. Our training services let you make the most of your NDT processes.
With cutting-edge solutions and support from a top-tier team, the experts at Fujifilm can help you find the ideal NDT technology for your X-ray weld inspections. Contact us today to learn more about our NDT solutions and how we can help you improve weld quality assurance.