What Is Reactive Maintenance?
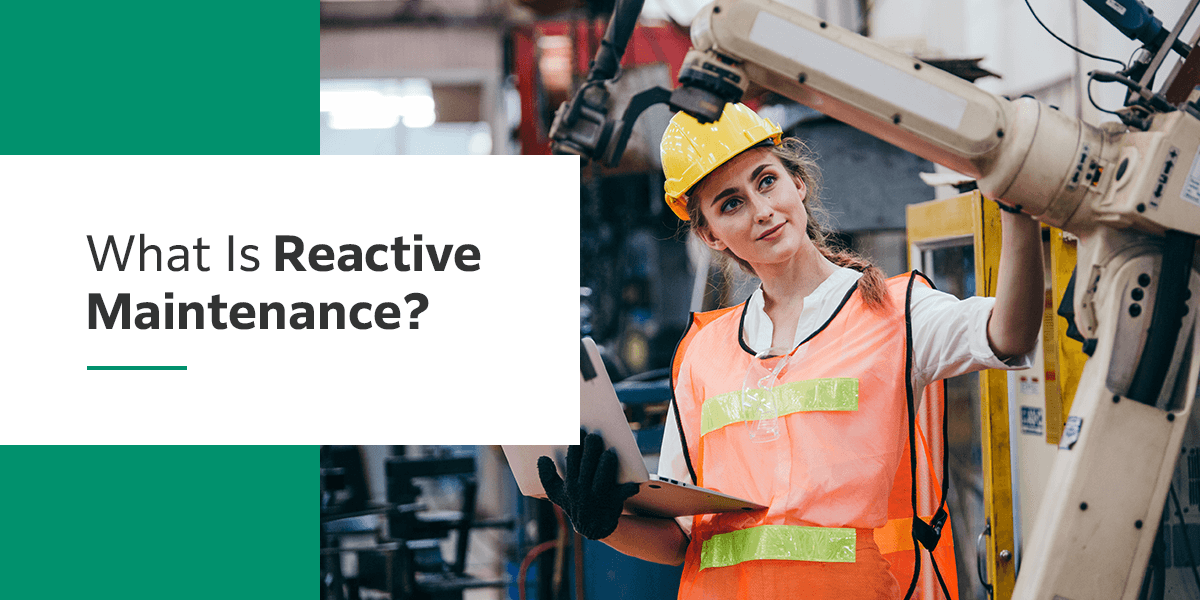
Jump to:
- Types of Reactive Maintenance
- When Should You Use a Reactive Maintenance Approach?
- Benefits of Reactive Maintenance
- Disadvantages of Reactive Maintenance
- Incorporate Non-Destructive Testing With Preventive Maintenance
When you take your car to the dealership or your local auto shop for routine service, you’re practicing preventive maintenance. By getting ahead of your car’s potential issues, you’re more likely to enjoy a smooth ride. But when your car breaks down, it’s time for reactive maintenance, which comes with its own set of perks.
No matter what kind of machinery you need to repair, reactive maintenance will be necessary at some point. Continue reading to learn more about reactive maintenance.
Types of Reactive Maintenance
Like any type of approach when maintaining machinery, reactive maintenance has its ups and downs. Additionally, utilizing only a reactive maintenance strategy may not be the smartest idea for all of your machines. As you learn more about reactive maintenance, you should consider which approaches will suit your applications best.
1. Breakdown Maintenance
This kind of reactive maintenance is when machines break down to the point where they become inoperable. This process may happen suddenly or over time, but either way, you must get repairs immediately or buy a new machine to continue operations. After all, the longer the machine is down, the slower production will get, and you could start losing profits. A backup machine is handy in breakdown maintenance situations.
With a plan, you can use breakdown maintenance to your advantage. Having a repair professional or a new machine on standby can help you swiftly overcome breakdown maintenance scenarios. Even during unexpected breakdowns, you’ll be able to proceed with operations as necessary, minimizing your losses.
2. Run-to-Failure Maintenance
Letting your machines fail on purpose is called run-to-failure maintenance. The machinery will have no maintenance or repairs throughout its lifetime, and it’ll continue to produce until it stops functioning. Generally, businesses won’t employ a run-to-failure type of reactive maintenance unless they have a clear plan for the machines or repairs.
For some companies, running the machines into the ground before any repairs start can save them cash on their bottom line. The run-to-failure method will let production continue without pause for preventive maintenance until the machine breaks down.
3. Corrective Maintenance
If one of your machines has a defect or a part isn’t functioning correctly, corrective maintenance might work for you. Conducting the repairs for the specific anomaly puts the machinery back on track and working perfectly. The benefit to corrective maintenance is that you can catch defects before they cause more significant problems and cost you more money.
The defining component of corrective maintenance is that you’re fixing a defect or an error in a working machine before it becomes a more prominent issue. In other words, you’re not repairing the entire machine. Many businesses practice corrective maintenance alongside other reactive maintenance approaches to keep their operations running.
4. Emergency Maintenance
An emergency maintenance strategy deals with sudden repairs that abruptly halt operations or may cause hazards. These failures are never planned and require such last-minute responses that most companies will benefit from keeping an emergency repair professional on standby to handle them. Because emergency maintenance can be dangerous, you may need to have an evacuation plan in place when the situation arises.
When Should You Use a Reactive Maintenance Approach?
Overall, reactive maintenance is an effective strategy for utilizing machines to their fullest potential and producing a maximum product output before total failure. The advantages of reactive maintenance are notable up to the point of failure. Then, downtime will happen. The reactive maintenance approach will be a planned strategy by the company to maximize machine lifespans and profits. Without a plan, reactive maintenance can cause significant setbacks for your company.
Benefits of Reactive Maintenance
There are many reasons why companies like using reactive maintenance strategies:
- Eliminates maintenance scheduling: Through reactive maintenance, you can continue operations without stopping for routine maintenance appointments. When practicing proactive maintenance, you must set aside time for repair technicians to inspect your machines and make necessary fixes. Skipping maintenance calls can help you stay on schedule.
- Reduces money spent on repairs: Paying maintenance professionals to make repairs every few months can put a dent in your budget. By choosing a reactive maintenance plan, you can use the resources you’d be spending on repairs for other business expenses. This additional money can be a significant help for some companies.
- Decreases operation downtime: When a repair technician comes to inspect and repair your equipment, you could be looking at days or weeks of downtime. To keep operations running as smoothly as possible, you may find that reactive maintenance is your best option. This way, you can continue day-to-day operations without maintenance-related hiccups.
Disadvantages of Reactive Maintenance
Of course, every plan has a few downsides — and reactive maintenance isn’t any different.
- Creates an unpredictable budget: When you follow a proactive maintenance plan, you can often predict how much you’ll spend on repair costs. With reactive maintenance, you won’t know your bill until a machine breaks down. This uncertainty may be a problem for budgeting purposes. A hefty bill at the wrong time can be a considerable financial concern.
- Leads to overtime: When equipment breaks down, you don’t just have to wait for the repairs to be made or a new machine to arrive. There’s also a significant amount of makeup time, where your employees have to work to get operations up to speed. This lost time may lead to workers coming on weekends or staying longer than they’re scheduled. As a result, you must pay overtime — and they become tired, unsatisfied workers.
- Causes inconvenience: Sometimes, machine breakdowns occur at the worst possible moments. Maybe your company is overwhelmed with orders to fill — and that’s when your most important equipment decides to stop working. The unexpected nature of reactive maintenance can lead to headaches, even when you attempt to plan around them.
Incorporate Non-Destructive Testing With Preventive Maintenance
The decision to use reactive maintenance in your operations depends on your unique situation. Using elements of both preventive and reactive maintenance in your facility may be your best bet. One essential component of preventive maintenance is non-destructive testing (NDT), which includes several techniques to ensure your parts function as intended. These techniques include but aren’t limited to:
Fujifilm provides high-quality radiographic testing products for various industries, such as aerospace and oil and gas, to spot defects and errors in products. This form of NDT can be a crucial part of a preventive maintenance approach, ensuring you can resolve issues without causing damage. If you’re considering a preventive maintenance strategy rather than a reactive maintenance plan, NDT systems from Fujifilm can help.
Contact Fujifilm for Your Non-Destructive Testing Needs
When you need a partner for quality NDT testing, Fujifilm has your company and your needs in mind. Fujifilm’s array of NDT equipment will help you ensure your parts and products work as they’re meant to and stay compliant. Fujifilm utilizes the latest technology to produce high-grade service every time, allowing you to keep up with your preventive maintenance schedule and serve your customer base.
Contact us today to learn more.