What Is Digital Radiography Testing in NDT?
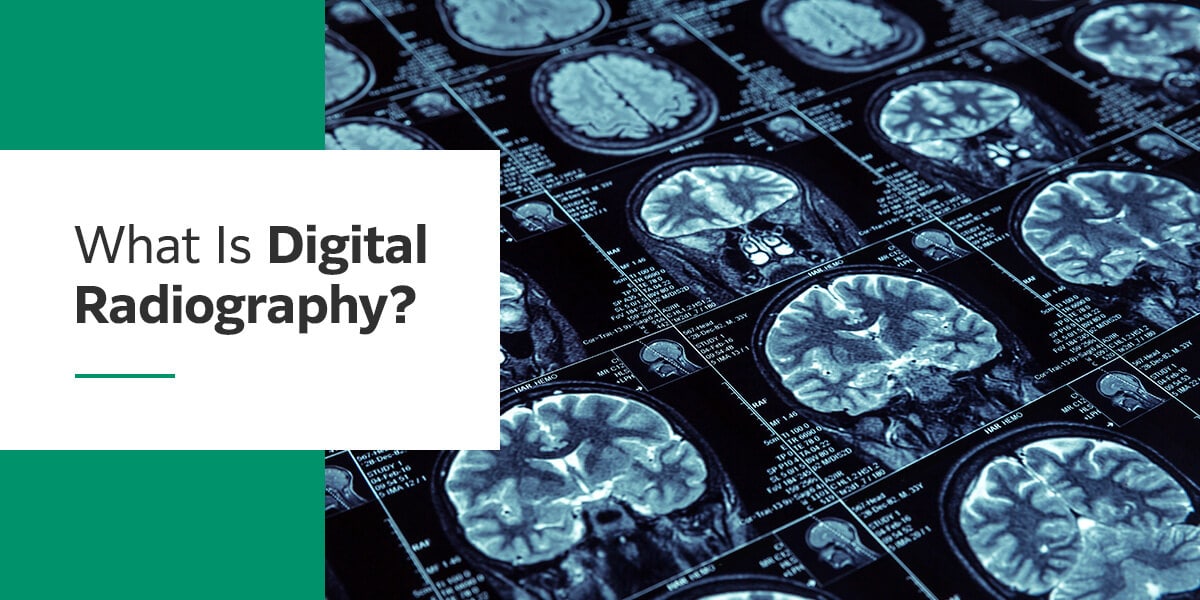
Jump to: Understanding Digital Radiography, Types of Digital Radiography, Digital Radiography vs. Traditional Film, Benefits of Digital Radiography, Digital Radiography Applications
Digital radiography, a technique used in non-destructive testing, excels due to its real-time applications, superior detail identifyability, and decreased inspection durations. Compared to computed radiography, it exhibits increased dose effectiveness, offering up to three times more. This efficiency, along with reduced noise during post-processing and a larger dose range, makes digital radiography a continuously growing preference among operators in non-destructive testing as technology advances.
Understanding Digital Radiography Testing
Digital radiography inspection is an innovative form of radiography using X-ray-sensitive plates to capture data for many fields, such as healthcare, aerospace, welding and more. Some applications for this solution include:
- Aerospace product examination.
- Detection of Corrosion Under Insulation (CUI) in petrochemical, oil and gas, and power generation industries.
- Detection of flow-accelerated corrosion (FAC).
- Healthcare examination.
- Foreign object detection.
- Casting and weld inspection.
- Composites and fibre-reinforced components inspection.
- Product and process development.
With direct radiography (DR), this data immediately gets transferred to a computer without needing an intermediate disc or cassette. The technology allows for real-time digital transfers, making the images and information available for analysis within seconds.
Digital radiography cassettes, required in computed radiography (CR), use state-of-the-art photo-simulated screens to capture X-ray imagery instead of traditional X-ray films, which can be time-consuming and expensive. A reader then converts the data from computer radiography cassettes into a digital format. Because digital radiography imaging plates are durable and flexible, they do not require a rigid holder.
Types of Digital Radiography
Compared to conventional radiography, digital radiography comprises discrete values, eliminating the requirement for darkroom procedures. Digital radiography may be indirect, semi-direct or direct. There are two primary types of digital radiography, including computed radiography and direct radiography.
Computed Radiography vs. Direct Digital Radiography
Computed Radiography
Computed radiography, also known as CR, uses photostimulable phosphor for an image receptor, held in a casing similar to traditional film. Computed radiography can harness radiation absorption to trap electrons at energy levels through the photostimulable luminescence process.
The computed radiology plate features a thin layer of phosphor grains, which get stimulated via X-ray radiation. This process will trap electrons in the lattice until the next round of illumination.
Exposing the computed radiography plate to a high-intensity laser allows the previously trapped electrons to return to their original valence bonds and emit violet light. Next, a photomultiplier tube interprets this light and converts it into an electric signal, which an analog-to-digital converter can map out and digitize onto a pixel matrix. You can reset the plate using white light, allowing you to reuse it if you handle it carefully.
Direct Digital Radiography
In contrast to computed radiography, direct digital radiography does not rely on intermediate processing to obtain digital signals. The two leading conversion methods include direct and indirect conversion. Indirect conversion received its name because it still uses a scintillator to transform X-rays into light before converting them to an electrical charge for readout.
During indirect conversion, X-ray photos react with a cesium iodide scintillator, which gets converted to light. The scintillator’s needle-like structures serve to minimize scatter during this process. Next, the light will reach a low-noise photodiode array, converting it into an electrical charge. These photodiodes represent single pixels, producing a digitally read electrical charge that then gets transferred to an image processor.
On the other hand, direct conversion refers to a technique that directly converts the absorbed X-ray into proportional electrical charges without the need for an intermediate scintillating process. Direct conversion requires the use of semiconductor material, producing electron-hole pairs proportional to the incident X-ray intensity. In most cases, the semiconductor used is amorphous selenium.
Digital Radiography vs. Traditional Film
German physics professor William Roentgen accidentally discovered traditional X-rays in 1895. Since then, they have been a valuable screening tool to help physicians diagnose multiple health conditions in medical settings. Digital radiography is also essential in many other functions, including aerospace product examination and casting and welding inspection.
As X-ray technology has continued advancing, it has become more accessible due to its lower costs. Digital radiography is a quick, efficient exam that can diagnose issues in medical and non-medical applications.
Conventional medical X-rays formerly required a large lead blanket or apron to shield the patient’s body from excess radiation. Digital radiography produces significantly less radiation than traditional X-rays while still providing high-quality results. While conventional X-rays are safe, digital radiography is even safer, especially in medical settings. The technology is much less likely to cause complications or medical issues from radiation exposure.
Digital radiography is also cost-effective because it doesn’t use expensive film or rely on costly materials to develop it. Digital X-rays offer nearly unlimited storage space because you can easily transfer the images onto a hard drive. Traditional film can make it challenging to efficiently store and access images, especially since they tend to degrade over time.
Digital radiography images do not experience these issues because you can access the archive anytime without the concern of image degradation. Whether in medical or non-medical applications, image quality is paramount. You need clear images to make a medical diagnosis or detect a structural anomaly.
With digital radiography, you can receive images in real-time and get results within seconds. If needed, you can also enlarge and enhance the image without adversely affecting its clarity or quality. Conventional film often becomes distorted or irregular when enlarged for potentially difficult-to-see issues.
To Summarize, some main advantages of digital X-rays over traditional film include:
- Reduce Radiation: Digital radiography can provide high-quality results while producing significantly less radiation.
- Cost-effective: Digital radiography doesn’t use expensive film or rely on costly materials to develop it.
- Easy & Unlimted Storage: Digital X-rays offer nearly unlimited storage space because you can easily transfer the images onto a hard drive.
- Receive Images Instantly: Receive images in real-time and get results within seconds.
- Enhance & Enlarge Images: Digital radiography allows you to enlarge and enhance images without adversely affecting its clarity or quality.
Benefits of Digital Radiography
Because digital radiography does not require the chemical processing of film, it is far more efficient and safer for the environment. Results with digital radiography are much quicker, improving productivity and enabling ease of storage and portability. While the benefits of digital radiography may vary from facility to facility and depend on your company’s unique needs, some of the most notable benefits of digital radiography include:
- Quality care: As medical diagnostic exams continue advancing, patients may have more concerns about these procedures’ potential side effects. Digital radiography uses significantly less radiation, making it a safer and more effective form of radiology. Additionally, digital radiography is highly accurate, with a low chance that you will need to retake an X-ray.
- Processing times: Processing times for traditional X-rays were time-consuming and expensive. You would need to wait for the film to develop in a darkroom before viewing the pictures. On the other hand, you can view the images gained from digital radiography in real-time, streamlining consultations, improving overall processing times and enhancing productivity for businesses and clients.
- Ease of use: Digital radiography requires minimal training and is relatively easy to use for many health care and aerospace professionals. It is a more straightforward process than traditional radiography.
- Imaging quality: Imaging quality is one of the central aspects of medical and non-medical applications, as each function needs clear and reliable images to complete a test or project. Digital radiography can produce higher-quality images than traditional imaging processes, allowing your business to focus on minor irregularities you might have otherwise missed. High-quality images are possible because digital radiography has specialized software that can electronically manipulate images for improved definition.
- Image sharing: Image sharing is also much quicker and more effective than manually or physically transporting physical X-ray films between departments and even facilities, expediting a professional’s ability to complete a project.
- Image storage: In addition to improved image sharing, storage is also much more efficient, significantly reducing the risk of misplaced or lost images. You can safely store digital radiography results on a hard drive, limiting access to unauthorized parties. Then, you can retrieve these images for review when needed.
- Resources: Another benefit of digital radiography is that it does not require chemical developers or film processors. Digital radiography requires a one-time installation investment, followed by routine maintenance to ensure the machinery runs smoothly. Additionally, digital radiography can help reduce labor costs for facilities as these digital X-rays do not take long to develop.
There are many advantages of implementing digital radiography in your healthcare setting. Digital radiography can improve a patient’s overall experience and outcomes while increasing medical professionals’ productivity and efficiency. Digital radiography is ideal for real-time applications and features shorter exposure times, enhanced detail detection and improved linearity. Outside a medical setting, additional benefits of digital radiography include:
- Improved signal-to-noise ratio
- Portable radiographic system
- Improved dynamic range with multiple thicknesses
- Immediate feedback
- Efficient electronic data transfers to customers
- Reduced downtime and increased productivity levels
- Possible to enlarge and enhance images for a detailed view
- Safer for the environment without the need for processing chemicals
- Use of defect-recognition software and analysis tool
5 Digital Radiography Applications
Digital radiography is a versatile tool with benefits across many industries. Some of the best-known digital radiography applications include the following.
1. Non-Destructive Testing
Non-destructive testing is an analysis technique that can evaluate various properties of a structure, system component or material for welding defects, characteristics anomalies, welding effects and more. NDT, also known as non-destructive evaluation or non-destructive inspection, does not damage the original part.
Non-destructive testing is an umbrella term to describe various inspection tools and methods. NDT is essential for commercial businesses to ensure critical infrastructure maintenance and avoid complications from a potential defect. NDT is common in professional applications, such as detecting faults in an industrial boiler, but it also plays a valuable role in medical facilities.
2. Medical Diagnoses
For medical professionals, digital radiography offers unparalleled image quality. Facilities that experience a high patient imaging workflow typically rely on digital radiography. This technology significantly increases image processing speed and subsequent accurate diagnoses, improving patient outcomes.
Another benefit of digital radiography is that it allows health professionals to store images digitally for remote viewing. Additionally, you can transfer photos to other facilities or patients who require an individual copy. Digital radiography can streamline appointments and diagnostic tests, meaning patients spend less time in the office, and doctors can promptly and accurately treat and diagnose patients.
3. Aerospace Product Examination
Product testing for aerospace applications is an essential product test to ensure quality results. Even a tiny error or unnoticed complication can be hazardous for aircraft, increasing the risk of accidents for pilots, personnel and passengers. Reliable testing, such as digital radiography, is one of the most crucial aspects of inspecting, outfitting and maintaining aircraft.
Digital radiography is also vital when designing and developing new aircraft. The technology can ensure an aircraft’s quality and raise its overall reliability rating to ensure safety. Digital radiography has become widely used in the aerospace industry and other settings, including industrial gas turbines and the oil and gas industry.
4. Corrosion Under Insulation Detection
Corrosion under insulation is a severe form of external decay that often occurs on insulated carbon and stainless steel and low-alloy steel equipment that operates below 175 degrees Fahrenheit or at high temperatures. In most cases, this phenomenon happens in petrochemical, offshore, refining and marine industries. If undetected or left untreated, it can cause dangerous complications.
Severe or untreated corrosion under insulation may increase the risk of prolonged downtime, equipment failure and leaks. In time, it may require expensive repairs or even entire replacements while also contributing to various environmental and safety concerns. Digital radiography can help effectively detect any instances of this issue.
5. Flow-Accelerated Corrosion
Another flaw digital radiography may be able to help detect is flow-accelerated corrosion. Flow-accelerated corrosion is a form of electrochemical degradation, sometimes aided by chemical dissolution and mass transfer. There are multiple forms of corrosion, including single-phase, dual-phase and liquid droplet impingement.
Flow-accelerated corrosion is the uncontrolled dissolution and transfer of iron oxides in a system cycle. Singe-phase locations refer to water, and dual-phase locations indicate water and stream. On the other hand, liquid droplet impingement is a form of corrosion that occurs when continual loss of material from a solid surface develops because of liquid droplets.
Choose Fujifilm for Premium Non-Destructive Testing
Fujifilm is a leading provider of superior non-destructive image quality due to our expertise in pioneering imaging products. We pride ourselves on implementing state-of-the-art technologies to offer the highest quality products and services to contribute to the advancement of technology, science and culture. Our team also aims to improve health and environmental protection. Contact us today for information on our Computed Radiography System, Digital Detector Array Panels, and Diagnostic Imaging Software.