What Is Electromagnetic Testing in NDT?
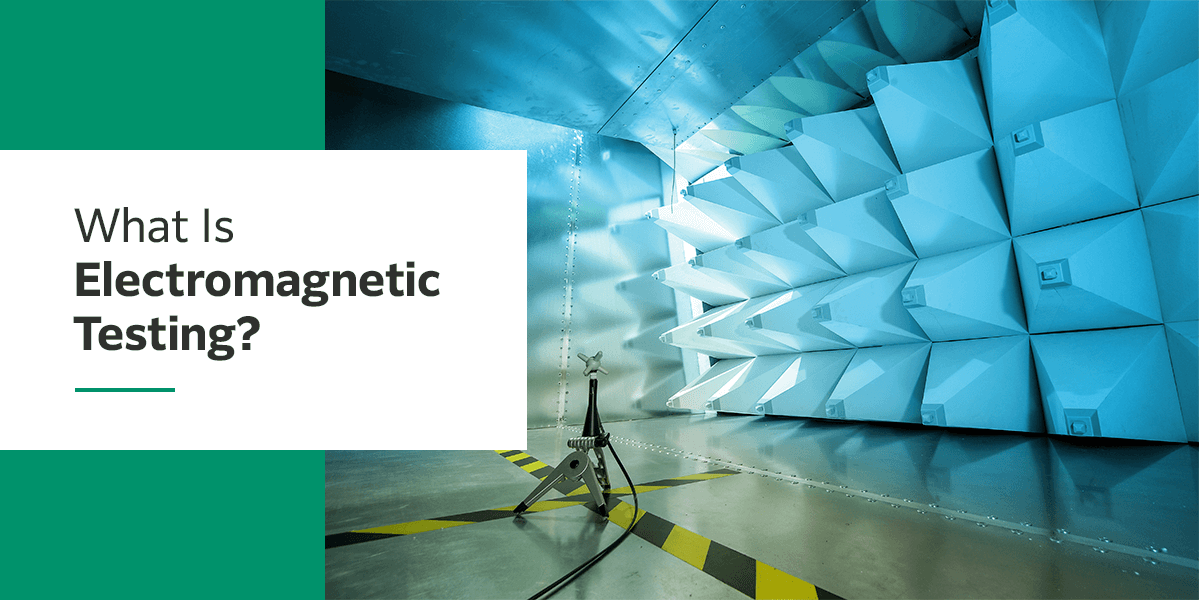
Jump to:
- What Is Electromagnetic Testing Used for?
- Electromagnetic Testing Methods
- Advantages of Electromagnetic Testing
- Disadvantages of Electromagnetic Testing
- Is Electromagnetic Testing Destructive?
Electromagnetic testing gives operations the power to test their components and materials for surface quality. Learn about this process and its benefits to see if it’s an ideal testing method for your organization.
What Is Electromagnetic Testing Used for?
An electromagnetic test is used to gauge the quality of an object throughout its lifespan. Eddy current testing is one of the more common types of electromagnetic testing, but there are a few methods professional testers use that apply electromagnetic principles.
Electromagnetism has the ability to test the external and internal condition of an object, making it a comprehensive quality test. When professionals use an electromagnetic test, they can observe and measure the object’s electromagnetic response. These responses can reveal corrosion, cracks, pitting, erosion and other features that may affect the quality of an object.
In industries where precision is essential to performance, electromagnetic testing is used throughout a component’s lifecycle. Engineers and manufacturers often use the process throughout development to test the quality of a design and ensure production meets design standards.
Some of the industries that use this testing include:
- Automotive
- Aerospace
- Construction
- Power generation
- Infrastructure
- Oil and gas
These sectors operate with tight tolerances for components to ensure the safety and function of their final products. Electromagnetic testing is a valuable resource for these industries to confirm the quality of components before adding them to projects.
Electromagnetic Testing Methods
There are four categories of electromagnetic testing.
Eddy Current Testing
Eddy current testing is based on the concepts of electromagnetic induction. Testers use an eddy current probe, which is a wire coil with an alternating current that creates an oscillating magnetic field. When the probe gets close to a conductive material, like a metal component, the eddy current flows through it and swirls through the material.
The flow in the metal component will create its own magnetic field and will interact with the probe through mutual inductance. If there are changes in the metal thickness or other defects in the component, the pattern or amplitude of the eddy current will change. A plotting instrument will register these changes for a professional to read.
Magnetic Flux Leakage (MFL) Testing
MFL testing identifies surface defects on ferromagnetic components, like steel, with a magnetic current. A professional tester will start an MFL test by using a strong magnet to create a magnetic field across the material. If the surface is free from defects, the field will spread throughout the surface without interruption.
When defects are present, the field will “leak” from the affected areas. MFL probes feature a detector between the magnet poles to identify the flux leakage field. The probe creates a magnetic circuit with the component, and the magnetic field saturates to a point where it can’t hold flux. When the flux leaks out, placed sensors can measure the leakage with a three-dimensional vector.
Magnetic Particle Inspection (MPI)
MPI, also referred to as magnetic particle testing (MPT), is a type of MFL testing. Like MFL testing, MPI starts with a professional magnetizing the object to be tested.
When the component has defects, the magnetic field will spread out from these imperfections and create a flux leakage field, as with MFL. The difference in these tests is what happens next. Rather than detecting the field with probes, the tester will spray magnetic particles over the surface of the component.
The particles professionals use often come in the form of a powder or liquid, and they’re usually a fluorescent color to make them highly visible. Once applied, the particles will gather around the flux leakage fields and make them visible to the human eye.
Alternating Current Field Measurement (ACFM)
In ACFM, a professional introduces an alternating current to a component to identify defects. When a surface is free from defects, the electrical field will flow without interruptions. If it runs into a crack or other defect, the current will flow around the ends and faces of the imperfection.
The current flowing through the component has a magnetic field above the surface, which will also experience changes with a defect. ACFM focuses on the magnitude of this magnetic field. A series of mathematical models can determine the size of a defect based on the behaviors of the magnetic field.
Advantages of Electromagnetic Testing
Electromagnetic induction tests are beneficial to operations for many reasons. These tests offer:
- Sensitivity: Electromagnetic tests are sensitive to all types of surface defects. Their sensitivity also allows them to detect surface characteristics through several layers and non-conductive surface coatings. If you want to apply an electromagnetic test to painted metal, the option is available.
- Accuracy: Conductivity measurements are highly accurate, so you gain a clear picture of the defects in your components.
- Portability: Electromagnetic testing equipment is generally easy to transport, allowing professionals to conduct the tests at your facilities. This fact is beneficial because you don’t have to risk damaging components when transporting them to testing locations.
- Automation: Some electromagnetic testing equipment offers automation technology to make the process more efficient and accurate. Automation often supports thorough documentation of defect detection for future reference.
Disadvantages of Electromagnetic Testing
While electromagnetic testing offers benefits, some of the disadvantages include:
- Requires conductivity: Only materials that can hold an electrical current are capable of undergoing an electromagnetic test. While many components work well with the various electromagnetic testing methods, it’s not a one-size-fits-all approach to quality control.
- Susceptible to magnetic permeability: Permeability is the measure of magnetization in a material once a magnetic field is applied. Permeability can change depending on the consistency of the material, and it can affect the readings of a test, particularly with eddy currents. This permeability is especially present in welds and ferromagnetic materials.
- Interpretation required: A professional must carefully examine current signals to identify where defects are located, so electromagnetic tests are not something you can perform independently.
Is Electromagnetic Testing Destructive?
Since electromagnetic testing does not cause damage to the components it’s used on, it is a form of non-destructive testing (NDT). Regardless of the method used, electromagnetic currents will not leave any changes behind once the process is complete.
NDT is often preferred over destructive testing because components can still be used following the test. NDT is often applied to objects in the middle of their lifecycle to determine if they’re still capable of performing their jobs.
Learn More About Non-Destructive Testing From Fujifilm
If you think electromagnetic NDT may be useful for your organization, learn more from Fujifilm. Our blog offers insight into the world of NDT, and our brand offers a range of NDT systems to support the process.