What Is the Contrast-to-Noise Ratio?
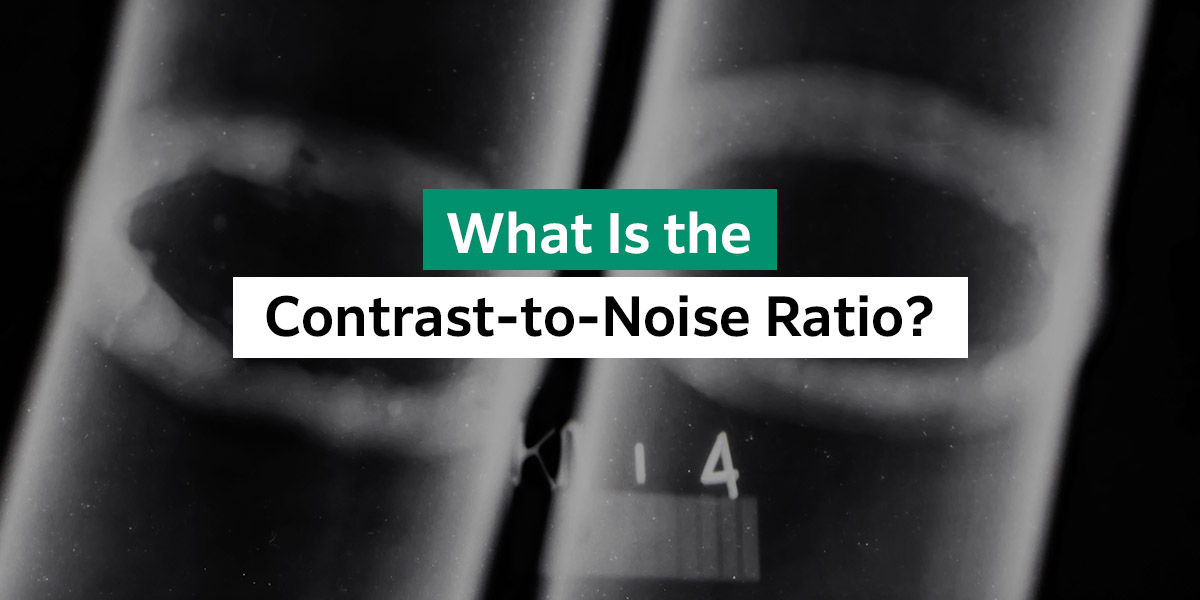
In non-destructive testing (NDT), a contrast-to-noise ratio (CNR) is the fundamental concept that assesses the quality of an image or signal from an inspection technique. It shows the relationship between the signal’s strength or contrast and the background noise level. Essentially, it measures image quality. While there will always be some noise in diagnostic imaging, it is crucial to find the right proportion. This balance with high contrast allows NDT technicians to identify any variations in material properties, discontinuities or defects accurately.
As technology advances, understanding CNR will help technicians refine the effectiveness and reliability of their imaging techniques in various applications.
What Is a CNR?
In non-destructive testing (NDT), the contrast-to-noise ratio refers to the measure you use to assess an image or signal’s quality during testing. The signal contrast magnitude is divided by the standard noise deviation in the image or signal. A higher rating indicates a strong, discernable signal and better detection reliability. CNR is calculated using the following formula:
- CNR = Signal Contrast / Noise
The signal contrast represents the difference in density or intensity between the defects or features of interest and the surrounding material. Noise refers to any unwanted variations in the image. These can result from sources of interference like electronic noise or scatter. Higher CNR indicates good image quality, signifying a strong contrast between the background noise and features of interest. Achieving a favorable CNR in NDT is crucial, representing accuracy in detecting and assessing material defects.
How Does Size and Contrast Affect Detection in NDT Imaging?
By considering the interplay between size and contrast, and employing the right inspection strategies, inspectors can enhance the effectiveness of defect detection in NDT imaging. This leads to better quality assurance and asset integrity management across NDT industries. Identifying smaller anomalies is easier with higher contrast, which enhances visibility and makes subtle variations more discernible. While larger structures may be more straightforward to identify, sufficient contrast can help to distinguish fine details and identify defects and distinguishable features.
How Does CNR Fit in With NDT?
CNR is a fundamental parameter in NDT. It influences the effectiveness of defect characterization and detection. It guides technicians in selecting the right NDT methods, optimizing imaging parameters and ensuring that images meet quality standards that yield reliable inspection results. NDT and CNR fit together in the following ways:
- Quantitative analysis: The quantitative analysis of CNR aids the standardization of NDT processes. This factor is critical in industries where defect sizing and characterization are essential.
- Image quality assessment: CNR measures image quality in NDT techniques as a quantitative calculation. Technicians use this measure to determine how well defects may stand out against background noise.
- Research and development: As new NDT technologies and techniques develop, CNR is the benchmark for assessing effectiveness in getting clear and discernible images.
- Quality control and assurance: CNR is a quality control method that ensures the images NDT Technicians acquire provide enough contrast for reliable assessment and detection.
- Certification and training: CNR considerations integrate into training programs for NDT Technicians because understanding how to optimize CNR ensures they can use imaging equipment effectively and interpret results correctly.
- Imaging parameter optimization: By using image processing techniques or adjusting exposure settings, NDT Technicians can enhance CNR, adding to the optimization efforts that improve defect detection capabilities.
- NDT method selection: Understanding the CNR characteristics of each NDT method as some methods can give you better CNR for specific types of defects or materials.
How Is a CNR Used in NDT?
The aerospace and automotive industries use CNR to verify component integrity and safety. In the energy sector, CNR analysis aids in identifying defects in infrastructure and manufacturing, showing user-dimensional variations. The CNR parameter finds use in various applications within NDT to detect defects, including:
- Guided wave testing: CNR helps to assess the clarity of guided wave signals, optimizing transducer parameters and signal processing techniques. It makes defect detection in pipelines and structures more accurate.
- Acoustic emission testing: CNR enhances the visibility of signals that show active defects or cracks in acoustic emission testing.
- Radiographic testing: CNR helps optimize exposure settings to assist technicians in assessing the visibility of cracks, defects or other irregularities.
- Eddy current testing: By evaluating the contrast between signals from discontinuities and background noise, CNR helps users adjust instrument settings to enhance sensitivity in eddy current testing.
- Computed tomography (CT): In CT imaging, CNR helps users distinguish between various materials to pickup subtle density differences.
- Neuron radiography: CNR creates enough contrast to help test material visibility with varying neutron absorption characteristics in neutron radiography.
- Visual inspection: When conducting visual inspections with borescopes, CNR helps users adjust lighting conditions to focus settings on enhancing surface anomalies.
- Magnetic particle testing: CNR improves surface and near-surface defect detection by optimizing the magnetizing and testing parameters.
- Ultrasonic testing: CNR helps to test echo and signal clarity from subsurface defects in ultrasonic testing. It is crucial to optimize transducer parameters and signal processing techniques to improve defect visibility.
How Can You Improve CNR in NDT?
To improve CNR in NDT, NDT technicians must make strategic adjustments that enhance signal clarity. The signal-to-noise ratio, the gray value in medical diagnostic imaging, indicates the standard deviation. As with CNR levels, higher values help NDT technicians better distinguish between elements on the scan. Key methods to achieve this include:
- Imaging parameters: Gain, exposure settings and filtering can lessen background noise and enhance signaling.
- Image processing: Different image processing algorithms can enhance contrast while reducing noise during post-processing.
- Assisted defect recognition: Use assisted defect recognition software to enhance accuracy, especially in the oil and gas industry.
- The right transducers: Use transducers with optimal frequency for specific defects and materials.
- Multiple techniques: Combining complementary NDT techniques allows NDT technicians to leverage their strengths and enhance inspection capabilities.
Choose Fujifilm for Your CNR and NDT Needs
In NDT, the CNR plays a vital role in assessing the quality of imaging techniques — particularly in radiographic testing. This metric optimizes inspection parameters, ensures reliable irregularity detection and enhances defect visibility. High CNR provides NDT technicians with clear visualization of structures while helping to characterize and detect defects in materials.
Fujifilm offers leading radiographic imaging technology, and we strive to help you achieve exceptional accuracy in every imaging inspection. We are a leader in NDT technology, providing you with the expertise and tools for reliable inspections. Contact us today to learn more about our NDT devices and get peace of mind about the quality of your CNR results.