How Is NDT Used in the Automotive Industry?
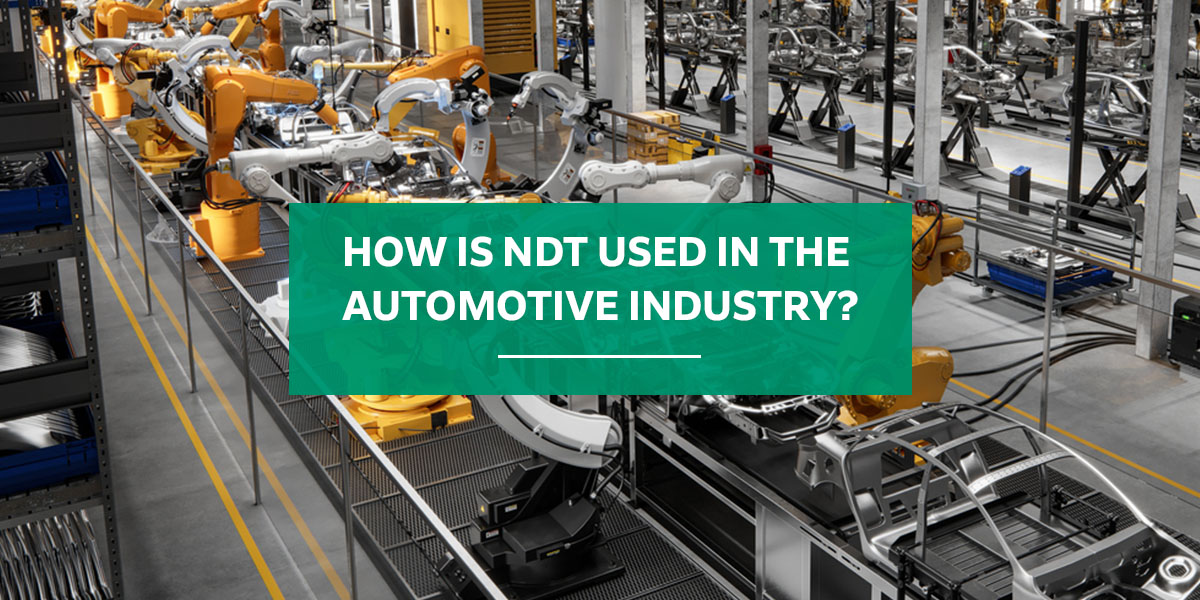
Jump to: Common Defects in the Automotive Industry, How is NDT Used in the Automotive Industry, How Can CR & DDA Help?
In an industry filled with high stakes and strict quality demands, automotive manufacturers consistently look for faster, more affordable ways of ensuring impeccable products. Non-destructive testing (NDT) is an ideal solution. This method allows you to test products without damaging the part itself.
There are different NDT testing methods, and they can be used on various parts and components. From speeding up production lines to improving accuracy and maintenance processes, NDT has a wide range of purposes and benefits. Learn more about NDT for the automotive industry.
Common Defects Within the Automotive Industry
Many consumers fall into the habit of seeing a car as a single unit or product, but anyone in the industry knows that cars have thousands of parts. One source puts the estimate at about 30,000 parts for the average consumer car. Each one of those parts can pose a threat. It might range from something simple, such as an odd rattling noise that annoys a driver, to something potentially dangerous that could cause accidents on the road.
Defects in these components can occur in any number of areas, like casting a metal part, welding two parts together or applying a coating. Issues may appear over time, as well, as parts erode, crack or otherwise degrade in response to environmental stressors. Some of the common car manufacturing defects that NDT can help detect include:
- Cracks and flaws in materials and surface treatments
- Issues from heat treatment, such as delayed or short quenches, shallow case depth or a lack of treatment
- Hardness variation due to problems during material mixing
- Thread and feature issues, such as missing or inaccurate features, broken taps or threads that are damaged, incorrect, oversized or undersized
- Improper assembly, like missing or improperly oriented components
- Poor welds with slag inclusions or inadequate penetration
Across stages like engineering, production and quality control, these parts call for care and precision. The non-invasive nature of NDT allows you to inspect parts for an array of defects, including material properties, component fabrication and damage.
How Is NDT Used to Detect Defects in the Automotive Industry?
You’ll find NDT across all stages of the automotive industry, including research and development (R&D), engineering, production and maintenance. It is a vital part of advancing technology, keeping the public safe, maximizing profits and meeting other goals.
Some of the ways businesses use non-destructive testing in the automotive industry include:
- Evaluating production methods and quality assurance: NDT can help assess the quality of production or manual processes. You might use it to spot-check an automated production line or inspect tasks prone to variation, like manual welds. NDT can provide clear, objective data to guide operations and provide quality verification. Since NDT doesn’t damage the part, you can use it on countless parts that will go into service. Confidently send components to customers without relying on a spot check from one that had to be destroyed.
- Improving defect identification: The human eye is far from perfect. Even the highest-quality images won’t help if the person reading them can’t spot a defect. NDR can be used alongside assisted defect recognition (ADR), which offers tools to help technicians read flaws accurately and improve defect detection. Automatic defect recognition adds artificial intelligence to identify defects.
- Meeting standards: The automotive industry is subject to strict quality regulations to keep the public safe, and NDT can help you meet them. Testing is also a great way to ensure you’re meeting internal quality standards that help you live up to your reputation. Some NDT methods are completely digital, so you don’t need to worry about physical files and can easily share results within the company.
- Improving production speed: Many forms of NDT are impressively fast. They can be used in-line in manufacturing processes and limit delays caused by destructive methods. Some types, like computed radiography (CR), can even reduce supply chain concerns from consumable supplies like film or liquid penetrants.
- Diagnosing problems: Since it doesn’t damage the part, NDT is often used in maintenance or repair processes. If someone suspects a vehicle or component of having a problem, an NDT image might reveal internal problems and help with servicing the part. It could be used for in-service vehicles, parts that fail quality inspections or even in R&D.
- Researching new technologies: R&D teams can use NDT to assess various new ideas or strategies. They might inspect a part after it comes off of newly configured fabrication equipment or scan a new material mixture used in a part. The tests can offer detailed insights that go beyond pass-fail assessments.
- Reducing costs: In many cases, NDT can save costs. You might save directly, with fewer testing supplies and destroyed parts, and indirectly, thanks to more efficient production, fewer recalls, better compliance and improved customer satisfaction.
How Can Computed Radiography and Digital Radiography Help?
Many types of NDT are available, based on qualities such as electromagnetic fields, fluorescent dyes, acoustic emissions and magnetic particles. Radiographic testing is a widely used option that relies on radiation to create an image, as a medical X-ray does. Computed radiography and digital detector arrays (DDAs) are two types of digital radiography, which modernize the classic X-ray system and eliminate expensive, time-consuming materials like film and development chemicals.
Digital radiography creates electronic readings for easy digital storage that can’t be lost or degrade over time. You can take readings in the field without waiting for film to develop, and you can use digital resources like ADR. For example, a digital system might be used to quickly diagnose a problem with a vehicle at various maintenance facilities or accurately scan high-precision parts at a fabrication plant.
CR provides a digital version of traditional X-ray systems, with the help of specialized phosphor image plates that can be reused many times. It offers a user-friendly interface and a chemical-free process and has less radiation and higher dynamic range than traditional film.
DDAs also offer digital radiographic testing, but they do away with the intermediary processing step that CR requires. This digital radiography system offers real-time readings and portable options. For large defects, DDA can be faster than CR systems.
With a low-cost investment and a process that works well with existing workflows, CR is an especially smart choice for low-volume applications and smaller businesses. DDAs can be an investment, but they’re faster and sometimes offer higher image quality. Their speed and portability make them a great option for in-field and high-volume applications.
Explore NDT Solutions From Fujifilm
Fujifilm is an industry leader in NDT imaging technologies, helping clients in the automotive industry and many others achieve quality, speed and flexibility through cost-effective solutions. These include the DynamIx HR2 CR system and our durable, high-resolution DDA systems, all backed by exceptional image processing technology.
Reach out to us today to learn more about how CR, DDA and other NDT solutions can help automotive businesses thrive.