Guide to Computed Radiography
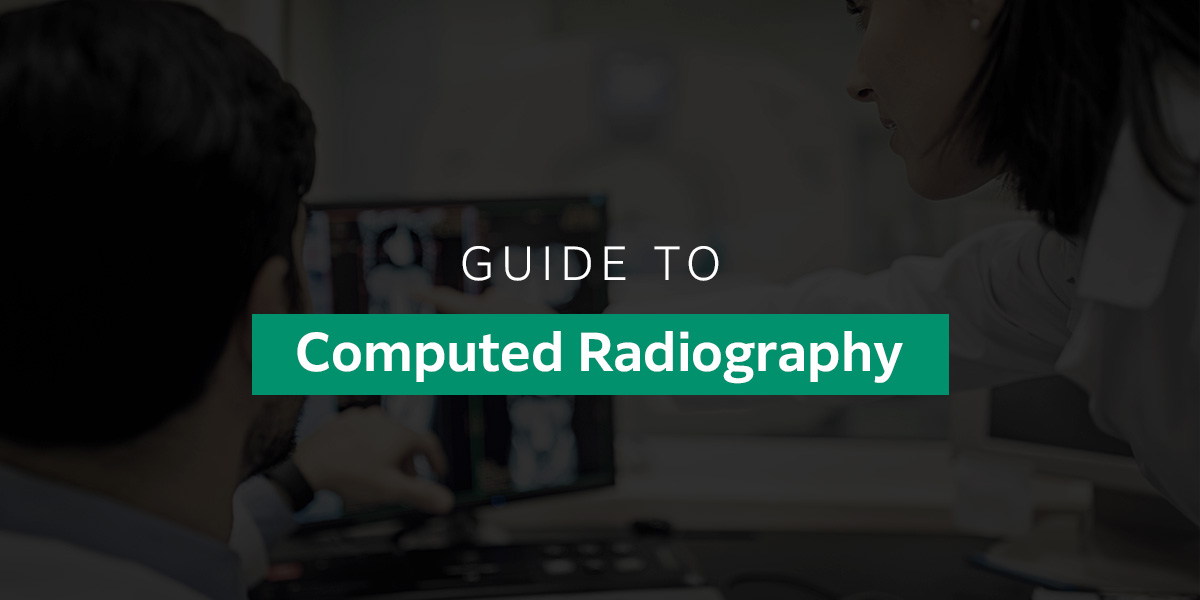
Jump to:
- What is Computed Radiography?
- Benefits of Computed Radiography
- Components of Computed Radiography
- How Does Computed Radiography Work?
- How is CR Different from Traditional X-Ray Testing?
- Applications of Computed Radiography
While conventional X-ray testing is still the preferred testing method for many businesses, newer non-destructive testing (NDT) methods can help your company more easily adhere to essential quality standards and industry regulations. Implementing digital technologies can help to bring your business into the 21st century.
If you’re looking to modernize your NDT processes, switching from conventional film X-ray testing to computed radiography (CR) may be ideal. CR has many advantages over traditional X-ray imaging in radiology applications, which can benefit your business.
This guide to using computed radiography for NDT covers everything you need to know about this technique and how it can enhance NDT operations.
What Is Computed Radiography?
Computed radiography (CR) is a form of digital radiography testing for NDT that replaces traditional X-ray film imaging. Unlike traditional X-ray systems, which use consumable film, CR systems use reusable photostimulable phosphor imaging plates (IPs) to capture images.
Upon radiation exposure, the IP captures the test object image similarly to how it would with film X-ray testing. The CR system skips the darkroom step. Instead, a reader unit reads the IP digitally, uploads the image to a computer for analysis, and erases the IP so it’s ready for the next image. The computer viewing software supports digital adjustments and enhancements to make analysis easier, while the CR system overall greatly reduces the amount of consumables required for film
The Benefits of Computed Radiography
Companies looking for a sustainable, cost-effective, non-destructive testing method can benefit from computed radiography. The main advantages of using CR include the following:
- Time savings: It only takes a few minutes to process images using CR technology, which boosts testing throughput and efficiency for technicians.
- Cost-effectiveness: Because CR IPs are reusable almost immediately after erasure, you can save money on imaging materials.
- Sustainability: Reusable IPs help reduce consumable usage. As a result, switching to CR can help businesses become more environmentally and financially sustainable.
- Chemical-free: While conventional X-ray radiography uses developer solution to produce images, CR systems are wholly digital. Switching to CR eliminates the need to store processing chemicals, freeing up space, and reducing overhead costs.
- User-friendly: Many operators find digital imaging software easier to work with than traditional film because they do not have to use darkroom equipment. Analysis is also easier because technicians can enhance image characteristics and remove background noise using the software.
- Image quality: Unlike with X-ray film, you can adjust CR images after processing to remove background noise and improve image clarity.
Computed radiography does have some disadvantages. The risk of damaged equipment is one of the main drawbacks, as CR cassettes are susceptible to damage from mishandling or abuse. CR systems also have more intensive maintenance needs than other digital radiography methods.
However, it is also true that CR imaging is more cost-effective than other digital systems, especially for businesses entering the digital NDT space for the first time. Carefully consider your organization’s needs before choosing an NDT system.
What Are the Components of Computed Radiography?
Computed radiography systems comprise several hardware and software components that perform each part of the imaging process.
These are the five main parts of a CR system:
- Radiographic generator: This device emits the necessary radiation to create an image on the IP. Often, existing generators are compatible with CR systems.
- Imaging plates (IPs): CR systems use cassettes containing reusable IPs rather than film. IPs can be erased and reused thousands of times, significantly reducing the need for consumables.
- Image reader: The reader replaces the darkroom of conventional X-ray testing. Rather than applying chemical solutions to an exposure to reveal the image, CR readers scan the IP, digitize the image, transfer it to the workstation, and erase the IP.
- Workstation: Most CR radiography systems use a standard PC to view, evaluate, and send digitized images.
- Software: Diagnostic imaging software provides a consolidated platform for storing, analyzing, and managing test images. This software streamlines file management and optimizes analysis processes.
Proper system maintenance is critical for ensuring high-quality test images. For example, you must erase IPs after each use because residual energy can create ghost images in later exposures. It’s also important to regularly erase unused IPs, which can capture faint images even while not in use.
How Does Computed Radiography Work?
The name “computed radiography” can be misleading because the actual imaging process includes minimal computations. In reality, it is more similar to traditional X-ray imaging than most computer processes.
Here’s a brief step-by-step explanation of how the process works.
1. Exposure
First, you expose the IP and test object to radiation to capture a latent image. This radiation may be X-rays or gamma rays, depending on your application. The energy from the radiation remains trapped in the IP’s phosphor layer.
Exposure time and image quality can vary depending on the type of IP you use. Other system components, like your scanner or display monitor, can also influence image quality.
2. Digitization
You then insert the cassette into the CR reader, which scans the IP by applying a focused laser beam to it. The IP emits a bright light in response, allowing the reader to pick up the image on the IP.
Using an analog-to-digital converter (ADC), the scanner turns the light into a digital signal, which it transfers to the computer. It then wipes the image from the IP using a high-intensity light source.
You can reuse the IP immediately after erasure if needed. Depending on the brand of IP and your specific application, you may be able to reuse one IP more than a thousand times.
3. Analysis
Once the converter has transferred the image to your workstation, you can begin analyzing the image for defects. Your diagnostic software allows you to manipulate the image for more in-depth analysis.
For example, you can alter the image and view it from different angles to get a clear, comprehensive view of the test object. Each software program has different features and capabilities, so it’s important to choose the right one for your business. Some helpful features to look for include the following:
- Automatic measurement tools
- Digital contrast normalization
- Smooth transitions between screens
- Traceability and reliable image quality assessment
- Flexible network configuration
Ideally, your analysis software will fit seamlessly into your CR system. Choosing one manufacturer and developer for all your system components is ideal for ensuring smooth integration.
Why Is Proper Technique Important for Computer Radiography?
Proper technique selection allows the software to seamlessly capture the image’s details with accurate contrast and resolution, making it easier to identify defects.
One of the most important technique factors is accurate exposure. Ensure the IP is positioned so the exposure creates a clear image. Underexposure can make it difficult to see, resulting in missed defects. Overexposure can distort defects, making it challenging to repair. The ideal positioning minimizes artifacts, enhances defect detection, and accurately represents the area of interest.
How Is Computed Radiography Different From Traditional X-Ray Testing?
CR radiography replaces film testing by digitizing the darkroom process in just a few steps. Like film, CR imaging uses cassette-based media and radiation to capture images — however, CR uses IPs instead of X-ray film.
Some other key differences between the two include the following:
- Consumables: Processing images using film requires darkroom chemicals, consistent, high-quality single-use film and other consumable materials. You can produce thousands or even tens of thousands of images through CR radiography with one set of IPs, a computer, and a CR reader.
- Environment: You need to keep X-ray images in a temperature- and humidity-controlled environment to prevent the film from warping or distortion. However, CR imaging eliminates the risk of image degradation by allowing you to store images on your workstation where environmental factors cannot impact them.
- Location: Film development must take place in a darkroom, which poses a challenge for many industrial facilities. As a result, many businesses using film testing must process their images off-site, which adds to the processing time. Fujifilm’s computed radiography systems easily fit into narrow spaces, saving you valuable floor space and time.
- Image control: While X-ray images are fixed, CR software solutions enable you to manipulate the scanned image after processing for greater visibility. This capability makes analysis significantly easier, reducing your chances of missing important defects.
- Labor intensity: Darkroom processing is significantly more labor-intensive than digitally processing and analyzing the same images. Switching to CR can help streamline processing and analysis while reducing labor costs.
While film testing has been the standard in image-based NDT for decades, transitioning to a CR system can help bring businesses into the modern era. Faster processing times and easier analysis enable companies to increase testing throughput and meet deadlines quicker, which is essential for staying competitive in today’s fast-paced world.
While X-ray testing has been the standard in image-based NDT for decades, transitioning to a CR system can help bring businesses into the modern era. Faster processing times and easier analysis enable companies to increase testing throughput and meet deadlines quicker, which is essential for staying competitive in today’s fast-paced world.
How Is Computed Radiography Different From Direct Digital Radiography?
While CR and direct digital radiography (DR) are both digital forms of NDT, they are different techniques. Here are the most important characteristics that set each method apart.
1. Equipment Requirements
The main difference between the two is in the equipment each system uses. IPs and DDAs both have layers that convert x-ray to light, but where essential CR equipment uses a separate reader to read the IPs, DR systems use flat-panel detectors or digital detector arrays (DDAs) to capture and read images.
After the IP captures the initial exposure, the NDT technician places it in a digital scanner where a laser beam scans the IP and converts the absorbed light into an image. Conversely, DR uses a combination of a light-emitting phosphor and built-in digital converter. This makes DDA is faster in theory, but the reality doesn’t always play out that way.
DDAs convert applied X-rays into electrical charges, which enter the transistors and produce a digital image in real time. It’s a common misconception that DDA is faster because that’s only true when looking at defects that do not have stringent requirements. Inspecting certain defects may call for geometric magnification depending on the specifications, which will require more shots to reach the necessary resolution.
2. Spatial Resolution
Another key difference is in the spatial resolution. CRs can go down to 25 um, but even the best DDAs only go to about 100 um, and it would take longer to get these smaller shots on a DDA. If you need to work with smaller defects, a CR would be quicker and more efficient.
3. Imaging Flexibility
One prominent difference that makes many companies choose CR is that DDA panels don’t wrap around pipes or round surfaces. To get them around these surfaces, you’d need to attach them using some kind of fixture. So, even though DDA may be faster with bigger defects, it still takes more time because of these little nuances. CR doesn’t have this issue.
CR IPs are flexible, allowing them to wrap around cylindrical or round surfaces easily. You can use these IPs to quickly take photos of difficult-to-reach areas for maximum efficiency and speedy results.
Industrial Applications of Computed Radiography
Computed radiography applications include almost any NDT process involving X-ray radiography, which can be useful for businesses in most industries. It’s typically the best technique for smaller companies with low-volume testing needs due to its low startup costs.
Some examples of industrial CR applications include the following.
Aerospace
The aerospace industry must adhere to stringent safety and quality regulations to protect passengers and cargo. Aircraft frequently travel through demanding environments that can accelerate wear and tear on sensitive internal components. Radiography testing is essential for catching defects early before they can lead to catastrophic failure.
CR can help manufacturers verify their airplanes’ safety by testing for subsurface defects. It’s also useful for identifying and monitoring signs of aircraft fatigue without causing additional damage to the plane’s delicate internal structures.
Automotive
Digital radiography techniques like CR and DR provide rapid results, which means they’re suitable for use in automotive manufacturing facilities. Implementing CR testing in-line speeds manufacturing by eliminating the delays common to destructive testing methods.
Because CR virtually eliminates consumable usage, it may also reduce supply chain issues that can interfere with timely vehicle production.
The speed of computed radiography can also help technicians improve repair and maintenance efficiency. Technicians can test the affected vehicle or component, then quickly pinpoint the source of the problem using advanced analysis software. Faster repairs can significantly improve customer satisfaction and increase profits.
Construction
Computed radiography can help construction companies modernize their operations by digitizing inspections and image management. Here’s how:
- Internal structure analysis: CR systems help construction professionals detect and identify internal structure characteristics such as voids, wire mesh, and cooling lines. They’re also especially valuable for inspections of castings, welds, and other components that are vital for the safety and efficiency of construction workers.
- Image manipulation capabilities: CR digital images allow technicians to adjust for clarity and identify defects more clearly. Certain software also comes with filters that make it easy to pick up defects quickly. It can save NDT technicians time and improve customer satisfaction.
- Compact footprint: Compared to film, digital imagery takes up less physical space and requires less environmental control. CR creates digital images of around 10 megabytes that fit easily onto most hard drives, DVDs, CDs, or network servers. Technicians can easily search for the file name and access the image — no need to spend extra time digging through drawers for old files.
- Communication capabilities: CR systems allow team members to communicate remotely. For instance, if a technician in another area needs a radiograph of a particular weld, you won’t have to arrange to travel or ship the physical image. Technicians can simply share the file via email or upload it onto a digital platform for easy viewing.
- Quicker inspections: Because CR takes less time to process images, it streamlines inspections. Site managers can keep projects moving along much quicker, allowing for faster project completion.
Gas and Oil
Digitizing the imaging process with CR can help gas and oil companies modernize and streamline testing procedures. It enables easier communication by allowing technicians to share, email and digitally store the images in minutes rather than over several hours. CR can also cut operational costs by eliminating the need for single-use consumables.
This digital radiography technology offers testing technicians a clear view into the health of their welds, piping and valves, enabling them to identify issues such as:
- Internal corrosion
- Corrosion under insulation (CUI)
- Poor quality welding
- Pipeline blockages
- Cracks and breakage
CR is especially powerful for this industry when combined with other advanced processing techniques like geometric magnification, which enables you to magnify small details in the image for greater visibility.
How Fujifilm’s Imaging Technologies Can Help
If you need advanced imaging solutions for your NDT application, the experts at Fujifilm can help you find the right system to meet your needs.
Streamline critical NDT applications such as parts inspection and site evaluation with the Fujifilm DynamIx HR2 CR system and DynamIx VU NDT imaging software.
DynamIx HR2
The DynamIx HR2 is a compact, user-friendly CR system suitable for use in any industry. Simply insert the image plate into the reader and process your images — the HR2 will eject the plate once the process is complete. Once your image is processed, you can perform multiple analysis operations quickly and easily, allowing you to obtain a comprehensive look into your test object.
The DynamIx HR2 reads imaging plates of various different sizes, including up to 152 centimeters long. Additionally, the device’s reading density spans from 25 to 200 μm. Custom options are also available for organizations with more specialized needs.
DynamIx VU
Our industry-leading NDT imaging software provides superior CR image quality and a wide dynamic range, allowing you to analyze test images with confidence in your results. This user-friendly software suite simplifies workflow and data management, streamlining inspections and enabling you to maximize return on investment (ROI).
DynamIx VU is suitable for inspecting many different types of components, including:
- Electronics: The software is suitable for use with sensitive electronic components like printed circuit boards (PCBs).
- Automotive: DynamIx VU can help you inspect mechanical parts like rotors, crankshafts and gearboxes.
- Aerospace: Inspect welds, investment casting and other mechanical components to ensure compliance with regulatory standards.
New, advanced features can help ensure more efficient inspection. DynamIx VU Thickness, our automatic measurement tool, allows oil and gas professionals to precisely determine pipe thickness by detecting both edges of the pipe wall and taking a focused measurement.
Additionally, DynamIx VU supports a wide variety of general and industry-specific standards for automated quality assessments. You can choose which parameters to test, and the software will do the rest.
Simplify NDT Analysis With Computed Radiography Solutions From Fujifilm
At Fujifilm, we provide cutting-edge NDT solutions for various industries and applications. Whether you need a digital radiography solution for oil and gas pipeline testing or construction site inspection, we can help you find the technology you need to get the job done right.
With more than 300 consolidated subsidiaries worldwide, we’re highly responsive to customer requests and passionate about providing innovative solutions for maximum value. We are the best resource for answering any questions you may have about CR and understanding your specific product needs.
Contact us today for more information about how our computed radiography systems can improve your operations, or browse all our NDT products to learn more about our offerings.