What Is Non-Destructive Testing (NDT)?
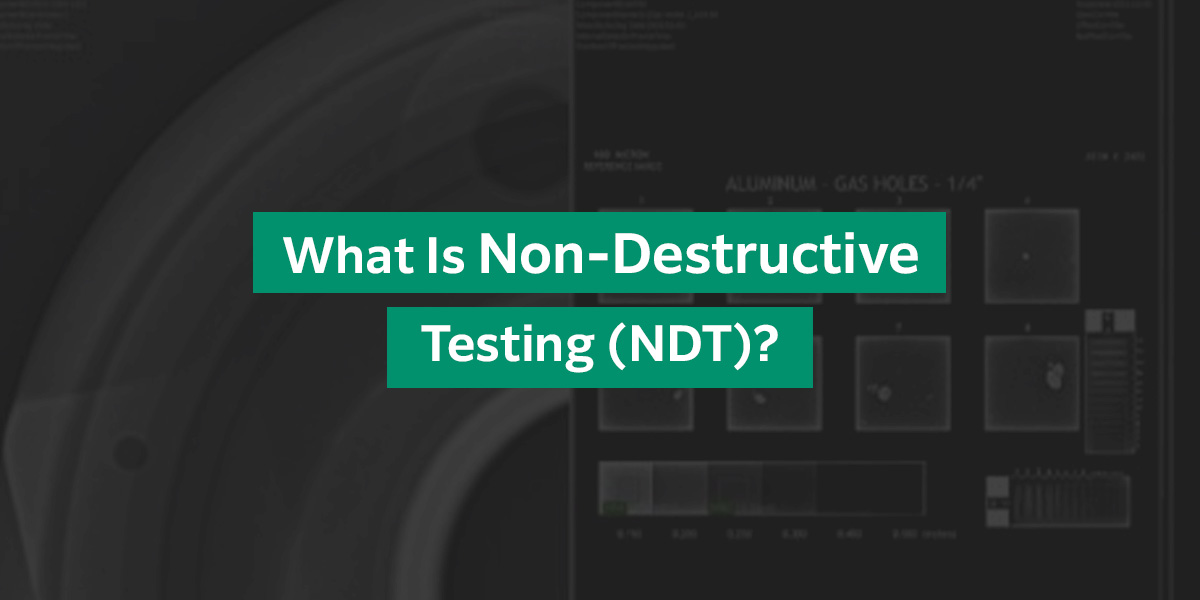
Jump to: What Does Non-Destructive Testing Mean?, NDT Methods, Industries Using NDT, NDT Training, Why Use Non-Destructive Testing Methods?
What Does Non-Destructive Testing Mean?
NDT’s meaning, non-destructive testing, refers to a group of testing approaches used to evaluate the safety, quality and integrity of materials, structures, components, or whole systems without damaging or altering their physical properties. Non-destructive evaluation has the following benefits:
- Data documentation: Most methods provide detailed, recordable data for analysis and future reference — facilitating trend analysis and predictive maintenance planning.
- Reduces downtime: NDT identifies defects during production or after installation, preventing costly downtime or catastrophic failure. It also helps in monitoring aging infrastructure for ongoing reliability.
- Mitigates environmental risks: This form of testing eliminates the need for destructive testing methods, reducing waste generation.
- Saves on costs and time: NDT saves on both costs and time by reducing the need for destructive testing — allowing for frequent inspections without incurring high material costs.
- Improves safety: This testing method deflects flaws, cracks or weaknesses before they lead to failure, protecting workers, equipment and the environment. It also ensures compliance with safety regulations and industry standards.
- Helps preserve equipment integrity: NDT is ideal for expensive or critical parts where destruction is not an option. It facilitates testing without damaging the materials or components, ensuring they remain in serviceable condition.
- Ensures quality control: Non-destructive testing provides detailed information about material properties and integrity, which helps maintain consistent manufacturing quality and reduce defects.
- Wide application range: NDT is suitable for various materials like metals and composites. It can inspect complex geometries and inaccessible areas using advanced methods, such as ultrasonic or radiographic testing.
Non-Destructive Testing and Inspection (NDT) Methods
Since NDT is such a broad term, you may want to know more about its main applications and the standard methods for conducting tests. There are several NDT methods and each can help you spot a material’s defects in different ways. Some of the most popular NDT techniques include leak testing, computed radiography testing, acoustic emission testing and liquid penetrant testing.
Common Types of Non-Destructive Testing Methods
Different NDT methods cater to different defect types, materials, structures and industry inspection requirements. Each method offers unique capabilities and sensitivity levels to ensure accurate, comprehensive inspection results. Choosing the right technique depends on factors like:
- Material type.
- Defect size.
- Component or structure accessibility.
- Regulatory standards.
- Cost-effectiveness.
NDT techniques used across various industries include:
- Radiographic testing: Radiographic testing locates component or system imperfections by using X-radiation or gamma-radiation — electromagnetic energy emitted by the nucleus. A radioactive isotope or X-ray generator sends radiation into a material and onto a detector, like a film. Technicians can then look at key readings from a shadowgraph created by the detector to help identify potential issues like density alterations.
- Visual testing: Visual testing (VT) is done by looking at an asset with the naked eye. Remote visual inspection devices can offer a more in-depth look at materials. Inspectors can identify cracks in the welds holding the boiler together, corrosion on the sides of the boiler and much more. There are several types of visual testing.
- Leak testing: When a structure or vessel leaks, leak testing can be used to study the leaks and identify defects. Technicians often conduct leak testing using soap bubble examinations, listening devices and pressure gauges.
- Acoustic emission testing: Testing with acoustic emissions can uncover potential imperfections and defects in assets. It identifies acoustic energy bursts and their arrival time, location, or intensity, which indicate defects.
- Ultrasonic testing: Ultrasonic testing transmits high-frequency waves into assets or materials to identify material property changes using pulse echoes. In this test, a technician sends sounds into an asset and measures the sound’s reverberations, as these sounds can help them identify surface imperfections.
- Magnetic particle testing: Using magnetic particle testing, technicians can identify material flaws by reviewing disruptions in its magnetic field’s flow. It involves inducing a magnetic field in an asset and placing iron particles on its surface. These particles show disruptions, giving visual indicators of imperfections’ locations.
- Liquid penetrant testing: Liquid penetrant testing starts with coating a material with a dye. Technicians then remove any extra solution from the asset’s surface. The remaining solution stays in cracks or breaks in the surface, revealing any defects. After finding these defects, technicians remove the fluorescent dye from the defects and examine them using ultraviolet light. With regular dyes, inspectors study the contrast between the dye and a developer.
- Eddy current testing: This is a form of electromagnetic testing. Eddy current testing involves technicians measuring a material’s magnetic field for the strength of eddy or electrical currents. Technicians will find electric current interruptions that identify material imperfections.
- Infrared or thermographic testing: Various materials absorb, emit and transmit infrared radiation based on their thermal properties. Infrared NDT detects these thermal patterns to identify irregularities, defects and material properties, particularly in aerospace, construction and manufacturing industries.
What Industries Is NDT Used In?
- Many industries utilize NDT techniques to ensure materials, systems, and assets are free from defects or imperfections. For example, companies employing manufacturing and fabrication processes often use NDT to confirm product reliability and integrity.Manufacturers also use NDT to keep their products consistent and better control their manufacturing processes. They may even combine multiple techniques for more comprehensive inspections.
While many companies use NDT in the manufacturing phase of their products, they can also use it to ensure their machinery and other essential assets are functioning correctly. For example, a mining company might have critical components and systems they need to perform at their best. NDT allows them to check these components without worrying about harming them.
Since there are so many types of tests, you can find several industries requiring particular kinds of NDTs to comply with industry- or company-specific regulations. For instance, the American Petroleum Institute lays out NDT codes and standards for oil and gas companies.
If you want to get a sense of how widely used NDT is, review some of the primary industries relying on NDT below:
-
- Mining: Mining relies on magnetic particle testing and ultrasonic testing to analyze machinery.
- Automotive: The automotive industry uses eddy current, visual, liquid penetrant, magnetic particle, radiographic and ultrasonic testing.
- Oil and gas: The oil and gas field inspections may use ultrasonic, eddy current and radiographic testing to assess weld quality, corrosion and cracks.
- Nuclear: Nuclear industries assess the safety and reliability of power plant operations with ultrasonic, eddy current, acoustic and radiographic testing.
- Aerospace: In aerospace operations, technicians will use ultrasonic, radiographic, magnetic particle, liquid penetrant and eddy current testing methods — ensuring structural integrity in aircraft components.
- Maritime operations: Maritime operations use ultrasonic or liquid penetrant testing to confirm the integrity of components on boats.
- Construction: There are various construction operations that use visual inspection, liquid penetrant, infrared and radiographic testing techniques to inspect welds, bridges, pipelines and more.
- Power generation operations: Power generation operations rely on visual inspection and ultrasonic and magnetic particle testing to inspect generators, valves, piping and vessels for problematic flaws.
Our NDT Training Services
Consider training staff to meet the industry requirements for Levels 1, 2 and 3 in Digital Radiography Certification, including SNT-TC-1A, ANSI/ASNT CP-189, CP105, FWGIDR, MAI and NAS410. Since learning how to implement and document NDT properly is crucial to your assets’ performance, you should turn to a company with the expertise to train employees properly. At Fujifilm, we offer NDT training services designed to help your team with various NDT applications.
When you turn to us for your NDT training needs, you can trust us to educate your employees properly about critical tests. We currently offer regional classes for employees without any NDT experience and Level One, Two or Three certified employees in RT/Film looking to become certified in Digital Radiography. We can even come to your facility and perform on-site training to help you reduce your production downtime.
Why Use Non-Destructive Testing Methods?
Using NDT techniques allows industries to assess internal and surface conditions accurately, leading to reliable products, systems and structures. It also leads to better safety, cost-effectiveness, and process efficiency in inspections, maintenance and manufacturing.
Whether you need to ensure the soundness of a structure or look for defects like linear, plantar or volumetric discontinuities, NDT methods are a reliable way to confirm whether it is necessary to take corrective action to maintain material quality control or make amendments for safety purposes.
Turn to Fujifilm for Your Non-Destructive Inspection Services
Using NDT techniques allows industries to assess internal and surface conditions accurately, leading to reliable products, systems and structures. It also leads to better safety, cost-effectiveness and process efficiency in inspections, maintenance and manufacturing. Whether you need to ensure the soundness of a structure or look for defects like linear, plantar or volumetric discontinuities, NDT methods are a reliable way to confirm whether it is necessary to take corrective action to maintain material quality control or make amendments for safety purposes.
If you need NDT services, you might be interested in Fujifilm. At Fujifilm, we’ve been a leading innovator in the NDT space for years. We specialize in providing digital radiography and conventional X-ray NDT products to help our customers discover any defects in their assets without harming the components they’re testing. When you partner with us, we’ll work with you to find the perfect solution from our product lineup, helping you stay on top of all your NDT needs.
Find out more about Fujifilm’s NDT products and services today, or contact us with any queries.
-